AUTOMAZIONE INDUSTRIALE
Case Study
White Label
L’utilizzo di mainsim nell’automazione industriale
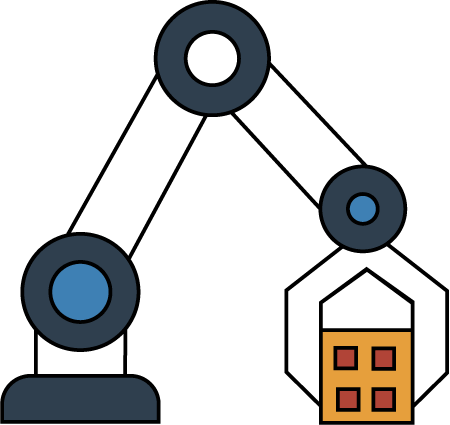
L’azienda
Fondata nel 2004, l’azienda (come ci riferiremo ad essa nel corso del presente case study per preservarne l’anonimato) rappresenta uno dei principali distributori di prodotti e servizi per i punti vendita dell’Europa meridionale.
Mediante l’utilizzo di sistemi integrati, l’azienda supporta il business dei propri clienti lungo l’intera catena distributiva, assicurando una gestione ottimale degli ordini e delle consegne.
L’esperienza, l’innovazione continua, le ampie infrastrutture, nonché la tecnologia applicata a tutte le operazioni di distribuzione, le hanno permesso di godere della continua fiducia da parte dei diversi stakeholeders.
Perchè White Label?
L’azienda a cui questo case study si riferisce ci ha chiesto di restare anonima. Nel rispetto della decisione del nostro cliente, il presente case study viene pubblicato senza alcun riferimento specifico all’azienda in questione e sotto etichetta generica.

La sfida
Disponendo di un numero elevato di macchinari industriali complessi, come nastri trasportatori e bracci rotanti, i processi manutentivi aziendali sono essenzialmente legati all’automazione industriale.
Prima di scegliere mainsim, la manutenzione era gestita con carta e penna. Le inefficienze che ne derivavano, in termini di tempo ma anche di acquisizione di dati utili alla corretta gestione dei processi, li ha spinti a cercare sul mercato un metodo più performante.
Il principale obiettivo del progetto era dunque quello di velocizzare il passaggio di informazioni e razionalizzare la gestione della manutenzione attraverso l’introduzione di un sistema informativo (SIM) che fosse in grado di snellire i processi e allo stesso tempo di favorire un approccio data-driven.
Settore: Logistica/Distribuzione
Location: Italia
Anno di implementazione: 2019
I numeri dell’azienda
55k punti vendita riforniti
118 depositi interregionali e locali
890 referenze
Gli obiettivi
Per raggiungere gli obiettivi imposti dal progetto, era necessario per prima cosa facilitare il più possibile l’introduzione del software all’interno delle procedure aziendali, permettendo a ciascuno dei manutentori di utilizzarlo in modo semplice e assicurare così la corretta registrazione dei dati tramite la piattaforma CMMS. In questo modo era possibile far fronte sia alle esigenze di consuntivazione che di semplificazione e gestione dei processi.
Dall’altro lato, doveva essere pensato un nuovo workflow che garantisse una gestione centralizzata del magazzino, attraverso le funzioni standard di mainsim.
Project Manager: Alberto Scaduto
Altri progetti gestiti da Alberto:
- Enel
- Sech
- Caleffi
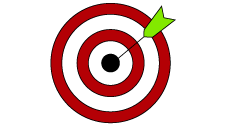
Obiettivo 1
Informatizzare i processi manutentivi per acquisire dati e generare report
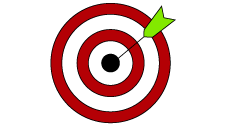
Obiettivo 2
Digitalizzare la gestione del magazzino ricambi integrandola all’interno del software
Il contesto
L’azienda adotta principalmente una strategia di manutenzione correttiva sui singoli componenti dei propri impianti, come per esempio nastri trasportatori e autopicker.
Alla manutenzione correttiva sono poi associati anche piccoli interventi di manutenzione programmata, come ad esempio il lavaggio degli autopicker o la lubrificazione dei meccanismi.
Da qui, l’esigenza di centralizzare il controllo del magazzino – per avere la certezza che siano sempre disponibili i materiali necessari alla sostituzione dei componenti guasti ed evitare dunque eccessivi tempi di fermo macchina – e di consuntivare in modo preciso e in tempo reale i materiali utilizzati nei singoli interventi.
Wizard: dalla richiesta rapida all’auto-manutenzione
Wizard è il modulo di richiesta rapida di mainsim. Attraverso una semplice procedura guidata, l’utente può identificare facilmente l’asset che sta ricercando e aprire una segnalazione di guasto in pochi passaggi e senza bisogno di digitare niente.
L’azienda ha optato però per un suo utilizzo alternativo, affiancando alla richiesta rapida un’opzione per l’auto-manutenzione dei propri impianti.
In poche parole, il manutentore che rileva un guasto non ancora segnalato può intervenire subito, senza passare necessariamente attraverso l’intera procedura di segnalazione e assegnazione del ticket, risparmiando tempo prezioso e riducendo al minimo i periodi di fermo macchina, pur senza rinunciare alla storicizzazione dell’intervento stesso e all’acquisizione dei dati.
L’analisi delle cause di guasto e la creazione di template pre-compilati per gli ordini di lavoro
Attraverso l’analisi delle cause di guasto, l’azienda è adesso in grado di snellire l’attività del supervisor nella compilazione e documentazione degli ordini di lavoro.
Poiché molti degli interventi manutentivi correttivi sono frequenti e ripetitivi, il sistema fornisce una check-list dei materiali consigliati in base al guasto segnalato. Questo permette al supervisor di risparmiare tempo nella documentazione del work order, ma anche di evitare errori e semplificare enormemente il lavoro di consuntivazione dei manutentori stessi.
Il mobile
Uno dei punti di forza del progetto è sicuramente l’utilizzo che viene fatto del mobile da parte dei manutentori.
Infatti, l’app per dispositivi mobili di mainsim permette ai manutentori di entrare in azione tenendo sempre a portata di mano documenti e check-list per facilitare il loro intervento.
Il manutentore non perde più tempo prezioso (e dati importanti) a consuntivare il lavoro a fine intervento, ma può farlo subito dal proprio telefono, trasmettendo i dati registrati durante l’attività – come per esempio i materiali utilizzati – semplicemente spuntandoli dalla lista allegata al work order.
Inoltre, grazie ad una gestione integrata dell’intero processo manutentivo, vengono acquisite in modo automatico tante altre informazioni, come per esempio i tempi di intervento, i tempi di fermo macchina e i costi, andando così a creare uno storico fondamentale per conoscere in modo più approfondito il comportamento dei propri asset e le loro performance.
Razionalizzare la gestione del magazzino con il QR-Code
L’aspetto relativo alla gestione del magazzino ricambi era di fondamentale importanza per il buon esito dell’intero progetto.
Per questo è stato necessario muoversi lungo due binari distinti.
Da una parte vi era la gestione dei materiali utilizzati durante gli interventi di manutenzione veri e propri, dall’altra vi era da gestire il monitoraggio dei rifornimenti e delle giacenze presenti in magazzino.
Per quanto riguarda il primo dei due aspetti che coinvolge dunque la necessità di consuntivare i materiali utilizzati durante un intervento, in modo tale da decurtarli dalle giacenze disponibili in magazzino, il manutentore può avvalersi dei template – con una lista dei materiali personalizzata in base al tipo di guasto – oppure semplicemente aggiungerli all’ordine di lavoro da una lista completa in fase di consuntivazione. In ogni caso, i materiali selezionati vengono automaticamente sottratti dalla quantità disponibile in magazzino.
Per ciò che coinvolge invece il secondo aspetto, relativo alla gestione dello stock presente in magazzino e quindi anche all’approvvigionamento e al monitoraggio delle giacenze, il QR-Code si è rivelato la carta vincente.
Applicato ai singoli scaffali del magazzino, ad ogni scaffalatura corrisponde un codice univoco associato ad un materiale preciso, in modo tale che sia sufficiente scannerizzare il talloncino per avere una completa visione dello stock disponibile in ogni momento.
In questo modo, piuttosto semplice ma estremamente efficace, è stato possibile centralizzare il controllo del magazzino ricambi integrandolo alla perfezione all’interno dei processi manutentivi, semplificando il workflow e migliorandone il controllo.
L’implementazione del progetto
Seguendo il metodo suggerito da mainsimWay, l’azienda ha proceduto con un’implementazione per step all’interno dei suoi depositi.
Il progetto pilota, avviato all’interno dell’HQ, è partito nell’autunno 2019 per estendersi poi ad altre filiali e via via a tutti i depositi presenti sul territorio italiano. Questo metodo di implementazione ha garantito all’azienda un maggiore controllo di ciascuna fase, rendendo l’adozione del CMMS più semplice e sicura per tutti.
Altri case studies che potrebbero interessarti:
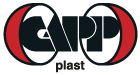
Capp Plast
La manutenzione è un costo diretto, indiretto o direttizzabile?
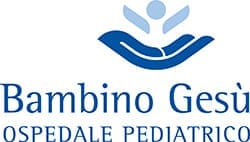
Ospedale Pediatrico Bambino Gesù
Asset management e gestione degli spazi
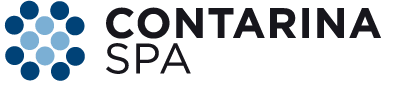
Contarina
L’ottimizzazione dei processi e la gestione dei dati con mainsim.
Unisciti agli esperti di manutenzione



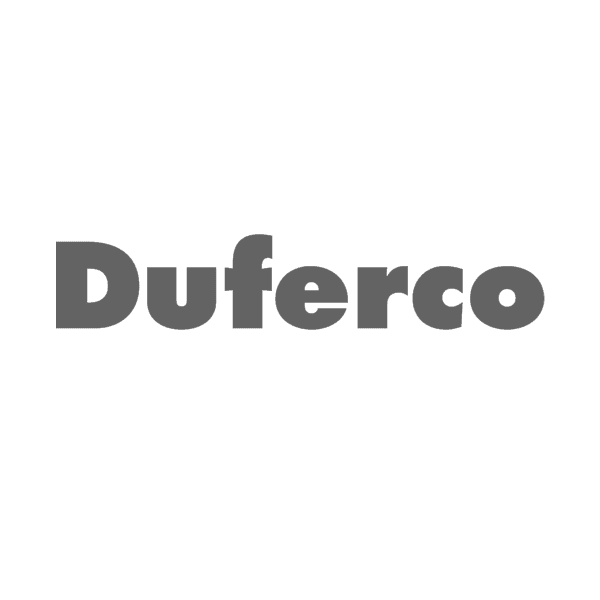

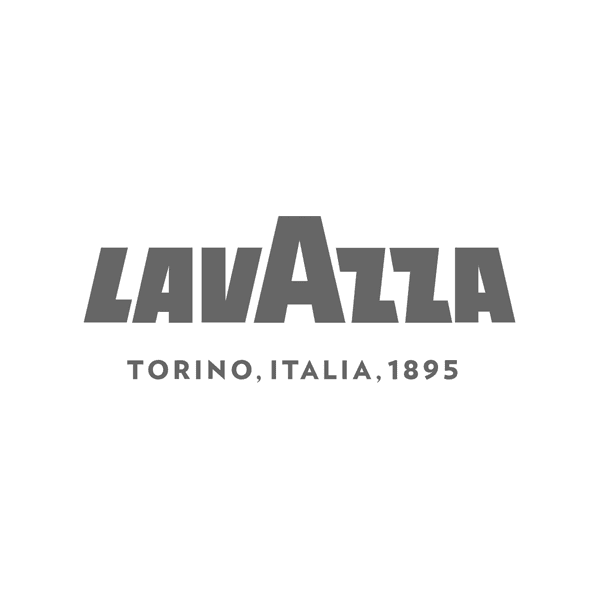

