Reliability-Centered Maintenance (RCM)
La guida completa alla manutenzione incentrata sull’affidabilità.
La Reliability-Centered Maintenance (RCM), in italiano conosciuta anche come Manutenzione Incentrata su l’Affidabilità, è il processo di perfezionamento continuo delle strategie di manutenzione applicate a macchinari e impianti che presentano le maggiori criticità all’interno di un’organizzazione.
L’obiettivo è quello di individuare la strategia più conveniente per massimizzare l’affidabilità (reliability) degli asset, minimizzando i costi di gestione.
In questa guida vediamo cos’è la Reliability-Centered Maintenance, perché dovresti considerare di adottare un approccio simile e come farlo.
Condividi l’articolo
Contenuto dell'articolo
- Cos’è la Reliability Centered Maintenance?
- Perché adottare un approccio alla manutenzione incentrato sull’affidabilità
- Obiettivi dell’RCM, la manutenzione incentrata sull’affidabilità
- I 7 principi della Reliability Centered Maintenance
- Applicare lo standard SAE JA101
- Attuare un programma di manutenzione incentrato sull’affidabilità
- Conclusioni
1. Cos’è la Reliability Centered Maintenance?
Il principio alla base dell’RCM è che ogni impianto e ogni macchinario richiedono un approccio diverso alla loro gestione.
Una manutenzione incentrata sull’affidabilità consente ai reparti di manutenzione di individuare quali sono gli asset più critici e stabilire per ciascuno di essi il programma di manutenzione più adeguato ed efficace.
Nel mondo della manutenzione si tende spesso a generalizzare, attribuendo ad alcune strategie di manutenzione un’importanza maggiore rispetto ad altre.
Non esistono però strategie più virtuose o meno virtuose, ne esistono semmai di più o meno convenienti e non è quasi mai auspicabile applicare a tutti gli asset lo stesso trattamento.
Il processo che porta a scegliere quale sia la migliore strategia da adottare per ciascun impianto è il fulcro della Reliability Centered Maintenance, la manutenzione incentrata sull’affidabilità.
Alcuni asset particolarmente critici potrebbero infatti richiedere un investimento per il monitoraggio continuo delle loro prestazioni attraverso tecnologie IoT e strategie di manutenzione predittiva, mentre per altri potrebbe essere più efficace dal punto di vista dei costi una semplice lettura periodica dei contatori, una strategia basata sulle condizioni o un programma di ispezioni regolari. Per altri ancora, lasciare semplicemente che le cose accadano potrebbe rivelarsi la scelta migliore.
Il punto è capire quale sia la strategia più conveniente.
2. Perché adottare un approccio alla manutenzione incentrato sull’affidabilità
Definizione di Reliability Centered Maintenance
L’Applied Research Laboratory di Penn State definisce la Reliability Centered Maintenance (RCM) come “un processo e una metodologia sistematici per determinare il piano di gestione della manutenzione più efficace ed efficiente per una piattaforma, un sistema o un componente specifico”.
Cos’è l’affidabilità in manutenzione:
L’affidabilità di un asset (in inglese reliability) è la possibilità che una risorsa continui ad operare e svolgere le sue funzioni in modo corretto ed efficace, evitando guasti e fermi macchina imprevisti o altre perdite di produzione.
Eliminare le inefficienze nel tuo programma di manutenzione preventiva
Manutenzione preventiva e manutenzione incentrata sull’affidabilità, sono spesso confuse tra loro.
Sebbene la manutenzione preventiva possa aiutarti a raggiungere alcuni obiettivi come un minor numero di guasti e di fermi macchina imprevisti, può anche far aumentare rapidamente i costi di manutenzione.
Gli studi più recenti sottolineano come il 60% delle attività di manutenzione preventiva finiscano per non aggiungere alcun valore agli asset, riducendosi ad una perdita di tempo e uno spreco di risorse.
Inoltre, possiamo considerare che il 70% dei guasti alle apparecchiature si verifica in modo casuale (non c’è per esempio una diretta correlazione con l’età del macchinario) rendendo in questo modo le strategie basate sul tempo non sempre ottimali, quando non del tutto inutili.
Puoi spendere meglio il budget di manutenzione
Sebbene i leader della manutenzione in tutto il mondo siano concordi nel riconoscere il valore della Reliability Centered Maintenance, nel settore industriale le viene spesso attribuita una fama poco lusinghiera per essere troppo resource-intensive e non sempre in grado di dare ottimi risultati.
Questo però è dovuto soprattutto ad un equivoco: non è possibile pensare di adottare un approccio RCM a tutti i tuoi asset, perché significherebbe analizzare un’enorme mole di dati e passare le giornate a elaborare strategie anziché metterle in pratica.
Non puoi pensare di applicare un approccio di Reliability Centered Maintenance a tutti i tuoi asset. Concentrati invece su quelli più critici.
3. Obiettivi dell’RCM, la manutenzione incentrata sull’affidabilità
Alcuni vantaggi della Reliability Centered Maintenance (RCM)
- Diminuzione dei costi associati alla manutenzione
- Incremento della produzione
- Incremento dei tempi di attività degli impianti
- Maggior conoscenza dei propri asset
- Maggior efficienza
- Ottimizzazione dei piani di manutenzione
- Migliore allocazione delle risorse e del budget destinato alla manutenzione
- Contenimento dei costi
- Risk management
Un esempio concreto di Reliability-Centered Maintenance per comprenderne le potenzialità.
Uno dei miei esempi preferiti quando si parla di manutenzione incentrata sull’affidabilità, compara la storia manutentiva di due aeroplani: il DC-8 e il DC-10/747-100.
Il DC-8: Il programma di manutenzione del DC-8 fu pianificato facendo ricorso ad una strategia di manutenzione preventiva tradizionale, basata sul tempo (time-based maintenance).
Un po’ come succede oggi con le nostre automobili, il programma di manutenzione del DC-8 prevedeva revisioni basate sul chilometraggio o sulle ore di volo, raggiunte le quali era necessario sostituire alcuni componenti con l’obiettivo di prevenirne il guasto. Significava sostituire delle parti dell’attrezzatura in dotazione al velivolo ancor prima che raggiungessero l’età stabilita.
Il DC-8 richiedeva la revisione di 339 componenti, per un valore complessivo di 4 milioni di ore di lavoro prima ancora di raggiungere le 20mila ore di volo. (E no, non c’è alcun refuso).
Il D-10: Il programma di manutenzione del D-10, invece, fu ricavato dall’applicazione dei metodi della Reliability Centered Maintenance.
Il velivolo richiedeva soltanto 66mila ore di lavoro e appena 7 componenti da revisionare prima di raggiungere le 20mila ore operative.
4. I sette principi della Reliability Centered Maintenace
Storia della Reliability-Centered Maintenance (RCM)
Il concetto di Reliability Centered Maintenance trova inizialmente spazio all’interno del settore aeronautico per poi essere adottato intorno alla metà degli anni ‘70 dalle forze armate statunitensi e dall’industria nucleare americana (negli anni ‘80).
Il contributo di John Mubray
La Reliability Centered Maintenance viene spesso accostata al nome di John Mubray.
Questo perché fu proprio Mubray ad adattare l’approccio Reliability Centered al mondo dell’industria in senso più ampio, dettando i principi che ne stanno alla base.
Negli anni sono emerse decine e decine di altre applicazioni simili, spesso anche fuorvianti e poco efficaci, fin quando non è stato stabilito lo standard RCM (SAE JA1011 – Evaluation Criteria for Reliability Centered Maintenance) che fornisce i criteri minimi che i processi devono rispettare per poter parlare di RCM.
Lo standard SAE JA1011
SAE sta per Società degli Ingegneri Automobilistici (in inglese Society of Automotive Engineers), ma non lasciare che questo ti tragga in inganno.
Lo standard tecnico SAE JA1011 (Criteri di valutazione per i processi di manutenzione incentrati sull’affidabilità – RCM) descrive i criteri minimi necessari per poter parlare di Reliability-Centered Maintenance.
Lo standard SAE JA1011 stato inizialmente sviluppato dall’industria dell’aviazione commerciale per migliorare la sicurezza e l’affidabilità delle proprie apparecchiature e nel tempo è divenuto lo standard da seguire quando si parla di Reliability Centered Maintenance (RCM).
Secondo SAE, per adottare un processo di manutenzione incentrato sull’affidabilità (RCM) è necessario rispondere a 7 domande in modo soddisfacente e rispettando la sequenza con cui sono poste.
Le 7 domande per lo standard RCM
- Identificare le funzioni del sistema
- Identificare le modalità di guasto
- Identificare le cause dei guasti
- Identificare gli effetti dei guasti
- Identificare le conseguenze dei guasti
- Indicare gli interventi preventivi
- Indicare le alternative
5. Applicare lo standard
Strumenti
La maggior parte delle organizzazioni che sviluppano un programma di manutenzione incentrato sull’affidabilità si servono di alcuni strumenti essenziali per la registrazione e l’analisi dei dati.
I principali strumenti che ti serviranno durante lo sviluppo di un programma di Reliabillity Centered Mainteenance sono:
- Modello FMEA/FMECA
L’FMEA, è l’acronimo inglese di Failure Modes and Effects Analysis. È un modello di analisi che consente di stabilire diversi livelli di criticità dei nostri asset attraverso lo studio delle modalità di guasto e degli effetti che si ripercuotono sui processi in termini di produzione, costi e sicurezza.
- Root Cause Analysis
L’analisi delle cause radice, o delle cause profonde, è uno strumento mutuato dall’industria automobilistica che consiste in un’analisi reiterativa delle cause che stanno alla radice dei guasti, con l’obiettivo finale di individuare colli di bottiglia e cali di performance.
- CMMS
Se ti stai chiedendo se esiste un modo semplice per ottenere tutti i dati che ti servono e dar loro un senso, il CMMS (Computerized Maintenance Management System) è l’unico strumento a cui devi pensare. Il CMMS è un software di manutenzione che ti permette di registrare tutte le informazioni sulle performance dei tuoi asset e del tuo team. I processi di manutenzione vengono standardizzati e divisi in fasi operative, e report personalizzati ti consentono di monitorare le metriche e i KPI legati alle performance dei tuoi asset (come l’MTBF o l’MTTR), i tempi legati al servizio e i costi suddivisi in manodopera, materiali, o beni e servizi se è previsto l’intervento di un fornitore.
Implementare i 7 principi della manutenzione RCM
L’implementazione di un programma di Reliability Centered Maintenance passa dunque attraverso i 7 principi definiti dallo standard SAE JA1011.
Si tratta dell’applicazione di alcuni criteri che scaturiscono dalle 7 domande fondamentali che dobbiamo porci e che insieme definiscono l’approccio RCM.
I 7 principi RCM – Criteri di valutazione
1. Cosa sono le funzioni e gli standard di prestazione associati al bene? (Quali sono le prestazioni del sistema/asset?)
Si tratta di definire le funzioni della risorsa o del sistema. Oltre alle funzioni che assolve, ci servono gli standard di prestazione, informazione che solitamente viene indicata dal produttore nella scheda tecnica dell’asset.
2. In che modo la risorsa può non rispondere alle funzioni richieste? (Quali sono le modalità di guasto?)
Ci viene richiesto di indicare le modalità di guasto conosciute di un macchinario, compresi tutti i suoi componenti. Ci servirà quanto meno una cronologia degli interventi, ancora meglio una cronologia dei guasti. Se la tua organizzazione usa un CMMS di buon livello, non sarà difficile estrapolare queste informazioni con report personalizzati e lo storico di tutte le attività svolte. In caso contrario, beh, qui servono dati. Spero che tu almeno abbia un foglio excel.
3. Quali sono le cause del guasto?
Dopo le modalità di guasto, dobbiamo analizzare le cause che stanno dietro all’errore. Anche qui, un CMMS può fare il lavoro sporco al posto tuo: il software CMMS mainsim, per esempio, introduce la Root Cause Analysis direttamente all’interno della scheda dell’asset e degli ordini di lavoro.
Scopri di più sulla Root Cause Analysis →
4. Cosa succede quando si verifica un guasto? (Quali sono gli effetti?)
Quali sono gli effetti del guasto? Ogni guasto potrebbe avere una ricaduta diversa sul sistema, sul processo o sulla qualità dei prodotti. Perdita di produzione, arresti non pianificati e costi elevati per la riparazione delle apparecchiature sono alcuni dei fattori più importanti da prendere in considerazione.
5. Quali sono le conseguenze del guasto? (Cosa succede quando si verifica un guasto?)
Ci sono rischi o criticità particolari che devono esseree prese in considerazione? In questo caso dobbiamo conoscere i rischi che si corrono in caso di guasto, rischi per la sicurezza dei lavoratori, per quella ambientale o rispetto agli standard che come azienda ci siamo imposti.
6. Quale compito sistematico può essere svolto in modo proattivo per prevenire, o ridurre in misura soddisfacente, le conseguenze del fallimento? (Cosa si dovrebbe fare per prevedere e prevenire i guasti?)
A seconda della criticità che abbiamo individuato durante la nostra analisi (potremmo aiutarci con un modello FMEA) possiamo considerare alcune attività che, in base alle informazioni in nostro possesso, ci permettono di gestire meglio i rischi associati al guasto. Potremmo pensare di implementare un programma di manutenzione preventiva, un’ispezione visiva o quant’altro, facendo attenzione a tarare bene la frequenza con cui vogliamo compierle.
Scopri di più sull’FMEA/FMECA →
7. Cosa si deve fare se non è possibile trovare un’attività proattiva adeguata? (Quali sono le alternative?)
L’ultima domanda è quella dove più spesso si incontrano i problemi. Cosa succede quando non è possibile trovare un’attività preventiva che sia conveniente? O ancora peggio quando non funziona? Se non funziona, vuol dire che stiamo perdendo tempo e spendendo male il nostro budget. Se non e conveniente, dovremmo capire meglio perché. Anche in questo caso un CMMS potrebbe aiutarci a trovare colli di bottiglia e inefficienze nel processo, per capire dove stiamo sbagliando. Infine, dovremmo prendere in considerazione politiche di manutenzione alternative, basate per esempio sulla condizione dell’asset.
Cosa vuoi monitorare?
Avere i dati è essenziale. Averne troppi può essere un problema.
Scarica la guida alle metriche e ai KPI di manutenzione. A te la scelta.
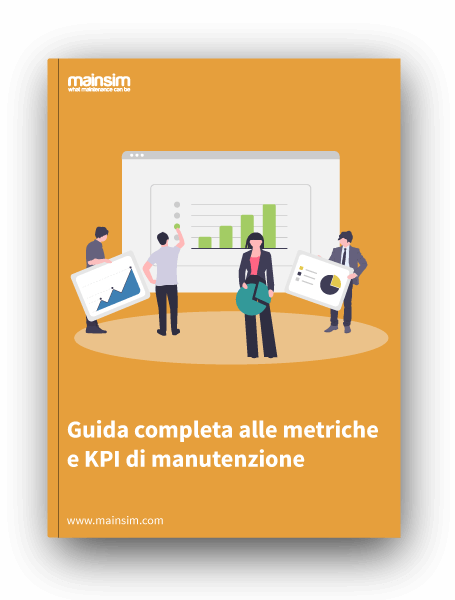
6. Attuare un programma di manutenzione incentrata sull’affidabilità
5 consigli per avviare un programma RCM
- Accetta i guasti: Non tutti i guasti possono essere evitati dal reparto manutenzione. Per fortuna, non è tanto il numero dei guasti ad essere importante, quanto invece il loro peso sul processo produttivo, sul budget di manutenzione e ovviamente sulla sicurezza dei lavoratori, ambientale, etc.)
- Molti guasti non sono dovuti all’età: tra il 70 e l’80% delle modalità di guasto non ha una diretta correlazione con l’età del macchinario. Se ti accorgi che l’impianto che stai analizzando presenta frequenti guasti che non sono riconducibili alla sua età o a quella dei suoi componenti, potresti provare a privilegiare una strategia basata sul monitoraggio delle condizioni.
- Alcuni guasti sono più importanti di altri: i programmi di manutenzione ben fatti, sono sempre basati sul rischio, sull’entità delle conseguenze e la probabilità di guasto.
- Non sprecare risorse: i piani di manutenzione ben fatti, non saprecano risorse. Riuscire a migliorare la comunicazione tra i reparti e con i fornitori riduce i tempi morti e aiuta le Operations a ottenere di più in meno tempo.
- I buoni piani di manutenzione migliorano col tempo: in questo sono come il vino buono. L’ottimizzazione di un piano di manutenzione è un processo lungo, fatto di piccole modifiche e test rapidi per sperimentare le soluzioni migliori.
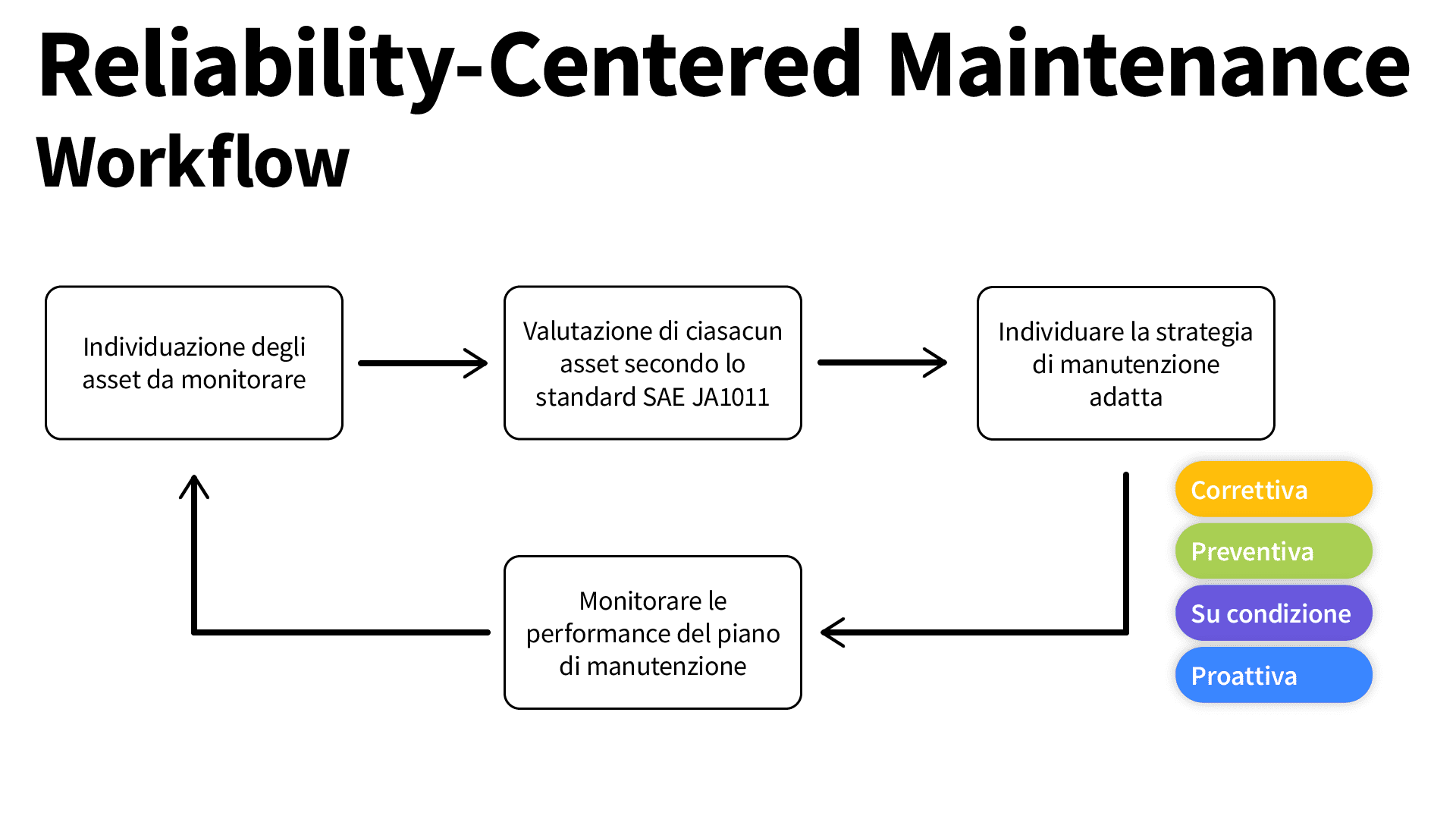
L’adozione di un programma di Reliability Centered Maintenance, inizia sempre dall’analisi.
Per prima cosa dobbiamo stabilire il perimetro all’interno del quale vogliamo operare, identificando quali sono gli asset più critici che meritano la nostra attenzione.
Ricorda, non è una buona idea concentrare le tue risorse su tutti gli asset presenti all’interno della tua organizzazione. All’inizio, prova invece a concentrarti soltanto su quelli più critici.
Stabiliti quali macchinari meritano la nostra attenzione, possiamo cominciare con l’esame della loro cronologia per comprendere quali sono i guasti più frequenti, quali effetti comportano sul processo, e i costi ad essi associati.
Una volta classificate le proprie risorse in base alla criticità e al rischio, possiamo concentrarci sulle azioni da intraprendere per migliorarne le prestazioni.
Questo comporta l’individuazione della strategia più appropriata per ogni risorsa (qui una panoramica delle principali strategie di manutenzione).
Un programma di manutenzione incentrato sull’affidabilità non si esaurisce però con l’implementazione di una strategia. Stabilita quale potrebbe essere la politica di manutenzione più conveniente per ogni asset, dobbiamo testarla.
Monitorare i risultati ottenuti ci consente di valutare la bontà delle azioni intraprese, e nel caso i risultati si dimostrino insufficienti o inferiori alle aspettative, cercare le alternative possibili.
Conclusioni
Un approccio alla manutenzione incentrato sull’affidabilità degli asset può farti ottenere risultati importanti in termini di efficienza e di contenimento dei costi.
L’RCM è un processo iterativo, composto da più fasi e non si esaurisce una volta completato il piano di manutenzione. Devi continuare a monitorare i risultati, se vuoi farlo funzionare. econtinuare a ottimizzare le tue strategie.
Per poter mettere appunto un programma RCM ti servono dati e informazioni che puoi ottenere in modo semplice con un CMMS ma per i quali dovrai penare molto di più se sei ancora bloccato al carta e penna o ai fogli excel.
Unisciti agli esperti
Oppure scopri il CMMS mainsim in meno di 3 minuti con questo video.