5S: cos’è e come implementarlo nella tua azienda
Il metodo 5S è conosciuto e apprezzato a livello mondiale. Adottato in prevalenza dalle grandi imprese multinazionali, rientra a pieno titolo nelle logiche di Lean Manufacturing insieme ad altri metodi ugualmente conosciuti come il TPM, il TQM o il Six Sigma.
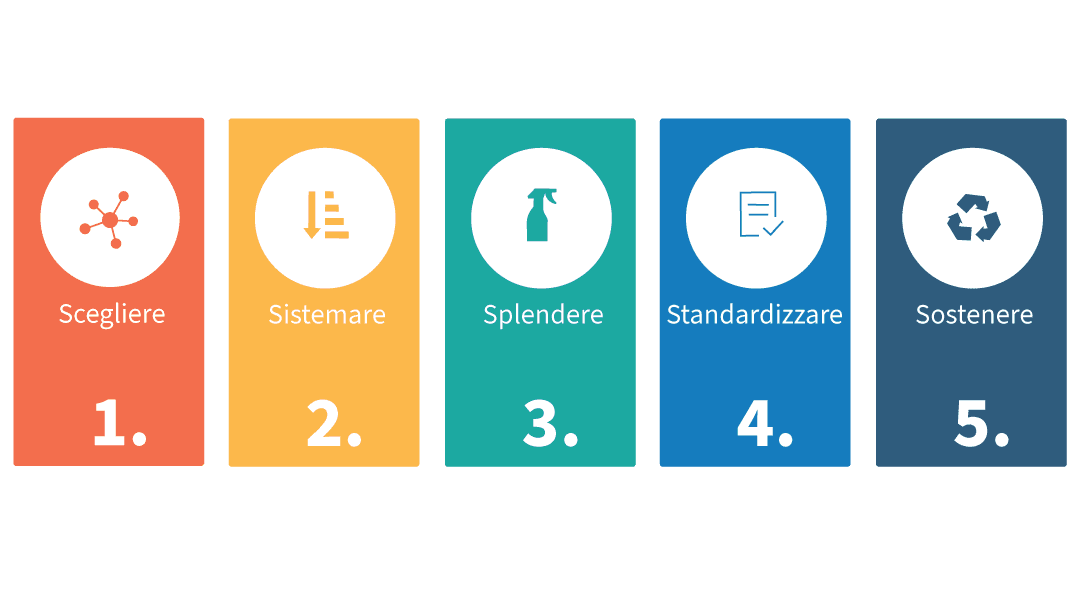
Cos’è il metodo 5S
Con il termine 5S si intende un metodo utilizzato da aziende e industrie di tutto il mondo, volto al raggiungimento dell’eccellenza produttiva tramite la riduzione degli sprechi, l’organizzazione e la pulizia del posto di lavoro.
Sebbene il metodo 5S sia impiegato in molti settori e reparti aziendali, dalla produzione fino agli uffici, rappresenta anche il primo degli otto pilastri del TPM (Total Productive Maintenance) e per questo motivo viene spesso associato a modelli produttivi come quelli storicamente utilizzati dall’azienda automobilistica giapponese Toyota.
La metodologia 5S nasce infatti dalla filosofia orientale di eliminare tutto ciò che rappresenta uno spreco, aspetto questo che fa rientrare le cinque S nell’ambito (oltre che nelle terminologie) della lean manufacturing e della lean production.
5S e TPM
L’implementazione delle 5S all’interno delle aziende moderne, rappresenta il punto di partenza per raggiungere il miglioramento continuo (dal giapponese Kaizen) delle attività produttive, con importanti ricadute positive sulla manutenzione di macchinari e impianti e sulla produttività aziendale. Al punto che il giapponese Seiichi Nakajima, padre tra le altre cose del metodo TPM, lo indica come la base di partenza e il primo degli otto pilastri che compongono il Total Productive Maintenance.
Vantaggi, benefici e obiettivi del sistema 5S
Coloro che hanno già adottato il sistema 5S all’interno delle proprie facility, riportano solitamente i seguenti vantaggi e benefici:
- Aspetto più ordinato e pulito della fabbrica, un aspetto importante soprattuto in caso di audit esterni o di visite aziendali da parte di clienti.
- Maggior coinvolgimento degli operatori nei processi di governo
- Riduzione dei tempi di lavoro e di produzione
- Maggior organizzazione del lavoro
- Macchine lasciate in condizioni migliori a fine turno
- Cambiamento culturale che coinvolge l’intera azienda
- Responsabilizzazione dei dipendenti
- Risparmio di tempo nella preparazione degli audit
- Miglioramento della sicurezza e riduzione degli incidenti
A partire dai benefici appena elencati è possibile dunque stabilire il principale obiettivo delle 5S: creare un luogo di lavoro efficiente e organizzato secondo regole condivise, per cui il lavoro di squadra rappresenta la condizione principale in funzione della riduzione dei tempi di lavoro e del miglioramento della produttività di tutti.
L’implementazione delle 5S all’interno di un’azienda produttiva, rappresenta infatti un semplice passo verso il miglioramento continuo dei processi, in grado di snellire il lavoro ed eliminare sprechi (di tempo, di energie e di risorse).
Un ambiente di lavoro organizzato secondo questi criteri, rientra perfettamente all’interno dei principi di lean production, in quanto in grado di contenere gli spazi di lavoro necessari, ridurre gli sforzi e i costi di produzione. Un’ulteriore ricaduta positiva dell’applicazione corretta del metodo 5S è rappresentata dal contenimento dei costi di manutenzione, sia in termini di tempo che di risorse. Questo significa interventi più rapidi e fermi macchina più brevi.
Inoltre, l’introduzione del metodo 5S, attraverso l’organizzazione dell’area di lavoro e semplici pratiche di manutenzione autonoma applicata a macchinari e impianti, permette di ridurre i difetti di produzione fino al 50% (Maasaki Imai).
Condividi l’articolo
Contenuto dell'articolo
Cos’è il metodo 5s
5s e TPM
Vantaggi, benefici e obiettivi del sistema 5s
Quali sono le 5 S?
Le 5 S
Le 5 S e il miglioramento continuo
Quali sono le 5 S?
Fin qui abbiamo visto obiettivi e benefici dell’implementazione del metodo 5 S, abbiamo discusso brevemente l’ambito in cui nasce e si sviluppa e detto come il sistema rientri nella filosofia lean e in un processo di miglioramento continuo (Kaizen).
Ma quali sono le 5 S e cosa indicano?
Le 5S si riferiscono a cinque termini giapponesi, ciascuno dei quali individua precise azioni da compiere per mettere in pratica questo metodo.
In giapponese, le 5S si riferiscono a:
- Seiri (Sort)
- Seiton (Straight)
- Seison (Shine)
- Seiketsu (Standardize)
- Shitsuke (Sustain)
In Italiano, possiamo tradurre le 5S in questo modo:
- Scegliere
- Sistemare
- Splendere
- Standardizzare
- Sostenere
Le 5S
Vediamo adesso nel dettaglio come applicare il metodo 5S attraverso l’osservazione di ciò che rappresenta ciascuno step.
- Separare (Sort): La prima delle 5S indica la rimozione dal banco di lavoro (o dalla scrivania nel caso di un ufficio) di tutti quegli strumenti che non sono strettamente necessari allo svolgimento della propria attività, creando quindi disturbo e perdite di tempo e risorse. La strategia più utilizzata per raggiungere questo obiettivo in ambito produttivo è quella del cartellino rosso, che consiste nell’assegnare un cartellino di colore rosso per identificare gli strumenti che, almeno potenzialmente, non sono strettamente necessari alla normale conduzione del lavoro. Una volta individuati quali di questi strumenti non sono di utilizzo comune (e dunque non servono, occupando spazio inutilmente), potranno essere rimossi dall’area di lavoro.
- Sistemare (Straight): Il secondo passo delle 5S è quello di sistemare e ordinare gli strumenti ancora presenti nell’area di lavoro, in modo tale che possano essere raggiunti con il minimo sforzo e senza perdere tempo a cercarli.
- Splendere (Shine): Il terzo punto del metodo 5S riguarda la pulizia dell’area di lavoro e del macchinario/impianto su cui si lavora. Ciò permette di responsabilizzare l’operatore (il quale deve essere considerato, appunto, responsabile per la propria postazione). Ma rientra in questo step, oltre alla pulizia, anche l’ispezione del macchinario e della postazione, che ci permette da una parte di individuare piccole anomalie prima che si trasformino in guasti veri e propri, e dall’altro di portare avanti giornalmente piccole attività di manutenzione autonoma, come la lubrificazione, per esempio, che nel lungo termine possono avere effetti importanti sulla conduzione degli assets.
- Standardizzazione (Standardize): La quarta colonna delle 5S riguarda l’obiettivo di standardizzazione di queste procedure, rendendole parte integrante delle operazioni da compiere su base giornaliera. È un passaggio, questo, di fondamentale importanza in quanto serve a creare regole condivise. Una buona idea è quella di aiutarsi con check-list, un semplice strumento in grado di creare una procedura standard facilmente consultabile dagli operatori.
- Sostenere (Sustain): Il quinto ed ultimo passo per l’applicazione delle 5S è in qualche modo legato al precedente. È necessario infatti far sì che queste procedure diventino parte integrante delle attività giornaliere, evitando quindi di vanificare gli sforzi compiuti a causa di un’applicazione saltuaria e incostante del metodo 5S.
Le 5S e il migioramento continuo
Il metodo delle 5S è spesso associato alle tecniche e ai sistemi di produzione lean, oltre che al miglioramento continuo. In particolare, le ultime due colonne della metodologia 5S (standardizzare e sostenere) mettono in luce come la procedura non sia da compiere soltanto una volta ogni tanto, ma bensì in modo costante e continuativo, in modo tale che tali pratiche siano di fatto assimilate nei processi e nelle attività giornaliere. Questo, nel tempo, può portare infatti all’individuazione di nuove inefficienze e nuovi sprechi, migliorando il processo e portando a quel miglioramento continuo (kaizen) proprio delle tecniche di lean production e lean manufacturing.
Esempio di applicazione delle 5S in aziende produttive
Come accennato in precedenza, uno degli approcci più usati per l’applicazione delle prime due delle 5S, è quello dell’applicazione sugli strumenti presenti all’interno dell’aria di lavoro di cartellini rossi (red-tag). Una volta segnate le attrezzature, potremo selezionare quelle che realmente ci servono e spostare in un’area appositamente dedicata le altre. Tutti i materiali che dopo i primi tre mesi non saranno ancora stati utilizzati (per cui hanno ancora il cartellino rosso) potranno essere eliminati.
Sebbene sia fondamentale che l’organizzazione degli spazi di lavoro venga dal basso e non sia imposta dalla direzione, come avviene anche per gli altri pilastri del TPM (Total Productive Maintenance) è necessario che il management riesca a comunicare in modo chiaro quali sono i vantaggi derivanti dall’implementazione delle 5S. Altrimenti esiste la possibilità, neanche troppo remota, che una tale attività sia percepita dalle maestranze come un’inutile perdita di tempo, mettendo a rischio l’intera operazione e, in ultima analisi, l’intero processo di adozione delle 5S.
L’esempio forse più calzante per spiegare quale sia l’effettivo vantaggio dell’applicazione del metodo 5S, resta forse quello del supermercato: grazie ai cartelli esposti in alto all’inizio e alla fine di ogni fila con scritti i prodotti ospitati, possiamo trovare in modo più semplice lo scompartimento che cerchiamo senza dover vagare su e giù per ore. Ecco, questo è un po’ il pensiero che sta alla base della filosofia 5S. Evitare che i nostri operatori, magazzinieri e operatori perdano tempo prezioso vagando in cerca dell’attrezzo che serve loro per portare a termine il lavoro.
Unisciti agli esperti
Oppure scopri il CMMS mainsim in meno di 3 minuti con questo video.