FMEA: modalità di guasto e analisi degli effetti.
L’FMEA (Failure Mode and Effects Analysis, in italiano Modalità di guasto e analisi degli effetti) è un metodo di analisi che permette alle aziende di determinare l’impatto che un potenziale guasto avrebbe su un prodotto o su un processo e valutarne i rischi.
L’analisi FMEA, insieme ad altre varianti come l’FMECA che vedremo in questo articolo, sono ampiamente utilizzate in settori come l’automotive, l’industria areonautica ed elettronica, ma anche in altri ambiti come l’healthcare e il facility management per la valutazione del rischio.
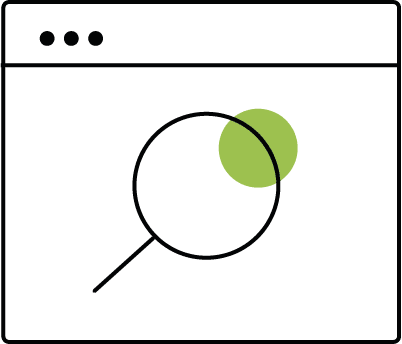
Cos’è l’FMEA: definizione.
L’FMEA è uno strumento di analisi che fornisce alle aziende la possibilità di individuare potenziali guasti prima ancora che si verifichino.
L’acronimo FMEA si riferisce alla sigla inglese Failure Mode and Effects Analysis, traducibile in italiano come Modalità di guasto e analisi degli effetti. In altre parole, la metodologia FMEA ci permette di valutare le probabilità che un evento (un guasto) accada e, se necessario, quali azioni intraprendere per fare sì che questa probabilità si abbassi contenendo i rischi.
In passato l’FMEA era utilizzato principalmente nel settore automotive e in quello aeronautico come strumento per la valutazione e la gestione dei rischi di guasto, ma si è presto esteso ovunque ci fosse un processo produttivo o fosse necessario valutare i rischi derivanti da un errore o da un malfunzionamento, fino alla sanità, dove oggi è spesso utilizzato per valutare gli effetti e i rischi sui pazienti.
A cosa serve l’FMEA?
I principali motivi per cui è importante effettuare una valutazione FMEA sono:
- Ricerca di difetti e potenziali problemi
- Valuatare i possiblii effetti generati dalle criticità e i rischi che essi comportano
- Individuare le possibili cause di guasto
Condividi l’articolo
Contenuto dell'articolo
- FMEA definizione
- Metodo FMEA: come funziona?
- Tipologie di analisi FMEA
- FMEA di progetto
- FMEA di processo
- FMEA/FMECA differenze
- FTA e FMEA: quale scegliere?
- Come fare una FMEA in 7 step
- Individuazione delle modalità di guasto
- Individuazione degli effetti
- Valutazione dei rischi
- Come calcolare l’RPN (RIsk Priority Number)
- FMEA esempio
- FMEA modello excel in italiano
- Vantaggi della valutazione del rischio
Il metodo FMEA come funziona?
Il metodo FMEA è considerato un approccio dal basso verso l’alto. L’analisi inizia con il mettere insieme i dati disponibili. Ogni componente del sistema viene esaminato attentamente per trovare tutte le probabili cause di guasto. Per ogni causa di guasto individuata, dovrebbero poi essere evidenziati i rispettivi effetti che questi guasti avrebbero sul processo.
Questo metodo di analisi, consente alle aziende di disporre di una mappa delle varie modalità di guasto che potrebbero occorrere, evidenziando gli effetti che questi possono generare, e infine organizzandoli in base all’impatto che avrebbero sull’azienda o sul processo all’interno di una tabella excel simile a quella sotto.
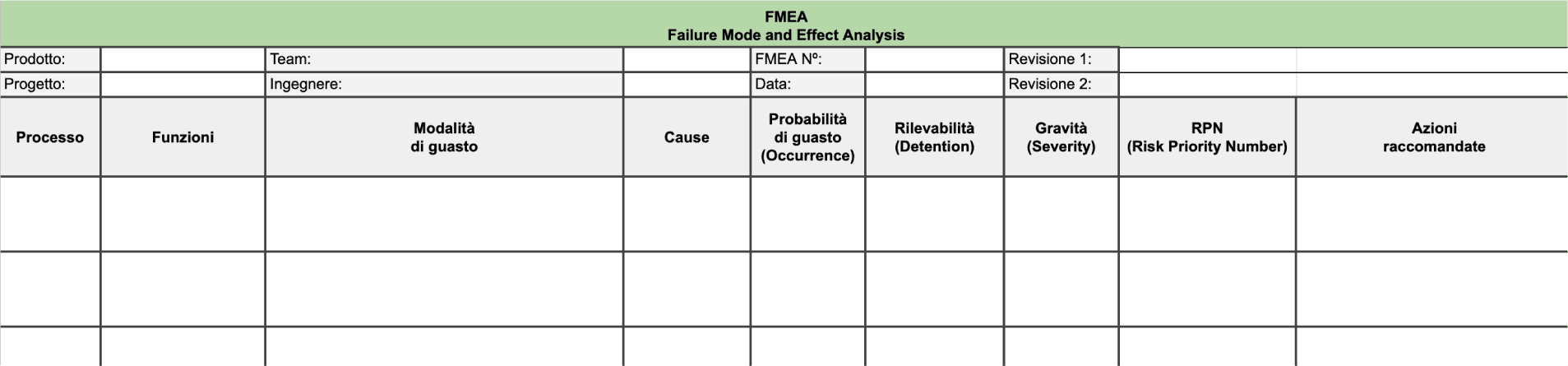
Scarica il modello FMEA excel in italiano.
Lo sviluppo di un processo FMEA è molto importante in ambito manutenzione, offrendo ai responsabili uno strumento di analisi per le cause di guasto e dei rischi che ne conseguono, aiutandoli dunque a stabilire le priorità e pianificare gli interventi di manutenzione preventiva in modo migliore.
Tipologie di analisi FMEA.
L’FMEA può essere ripartito in diverse tipologie a seconda del campo applicativo e della tipologia di indagine che vogliamo portare avanti. Le due categorie principali sono FMEA di progetto (DFMEA, Design FMEA) e FMEA di processo (PFMEA, Process FMEA). Ognuna di queste categorie si concentra su momenti specifici di un processo.
FMEA di progetto (DFMEA)
Questa particolare analisi FMEA si concentra sugli aspetti di progettazione di un dispositivo, di un prodotto o di un servizio. In particolare, questa analisi viene svolta a monte del processo, per testare nuove idee di prodotto prima che siano immesse sul mercato o comunque in scenari di vita reale.
FMEA di processo (PFMEA)
L’analisi FMEA di processo (PFMEA) differisce da quella di design nella misura in cui esamina processi e procedure che un’azienda sta già seguendo. Non si tratta dunque di una fase di prototipazione o di progettazione, ma di affrontare potenziali criticità che possono avere effetti sulle normali operazioni. Alcuni esempi di attuazione dell’FMEA di processo riguardano per esempio gli errori umani o i rischi per l’ambiente e la sicurezza.
Un’altra differenza molto importante da sottolineare tra DFMEA e FMEA di processo è il ruolo dei dati storici nell’analisi: mentre per il primo in genere non si dispone di molti dati, quando si parla di FMEA di processo è molto utile fare riferimento ai dati storici in nostro possesso per migliorare l’efficacia dell’analisi.
FMEA e FMECA differenze.
Molto spesso si crea confusione tra le sigle FMEA/FMECA. Come lo abbiamo definito, l’FMEA è un approccio metodologico che identifica tutte le possibili modalità di guasto e ne analizza gli effetti che essi possono avere sul sistema nel suo complesso.
In questo senso, l’FMECA compie un ulteriore passo avanti nell’analisi, valutando non solo gli effetti e i rischi, ma associando anche ad ogni possibile modalità di guasto una priorità in base a questo fattore di rischio.
Sebbene dunque FMEA e FMECA siano strumenti molto simili e strettamente correlati, ci sono alcune differenze. Mentre FMEA può essere descritto come uno strumento qualitativo, l’FMECA è uno strumento quantitativo che, oltre a descrivere le modalità di guasto e i loro effetti, si propone di classificare questi effetti in base alla loro gravità, determinando quali sono gli elementi di rischio più elevato e descrivendo le azioni correttive da intraprendere.
Per fare ciò, l’FMECA si avvale del numero di priorità di rischio (RPN, dall’inglese Risk Priority Number), il quale permette di classificare la criticità di ogni asset.
È facile immaginare come questo ulteriore sviluppo dell’FMECA rispetto all’FMEA assuma un’importanza maggiore per chiunque si occupi di gestione della manutenzione, permettendogli di stabilire priorità sulla base dei fattori di rischio, razionalizzare le attività e sviluppare piani di manutenzione migliori.
FTA e FMEA. Quale scegliere?
Qual è la differenza tra FTA e FMEA?
FTA e FMEA sono due tipi di analisi diverse. La prima tratta l’analisi delle condizioni che portano al verificarsi di un guasto (cause di guasto), la seconda è invece descritta come l’analisi delle modalità di guasto e degli effetti che essi generano e serve a valutare il rischio e prioritizzare determinate azioni preventive/correttive.
Vediamo più nel dettaglio quali sono le differenze tra FMEA e FTA.
L’FMEA è una tecnica dal basso verso l’alto che esamina le modalità di guasto dei componenti di un prodotto, di un processo, di un sistema, tracciando tutti gli effetti che ciascuno di questi guasti può generare. In questo senso l’FMEA è una modello basato su un rapporto di causa-effetto.
L’FTA (Fault Tree Analysis) riguarda invece l’identificazione e l’analisi delle condizioni che portano al verificarsi di un evento. Al contrario dell’FMEA, l’FTA è una tecnica dall’alto verso il basso e più precisamente un modello effetto-causa, in quanto parte da un evento che si è verificato tornando indietro ad identificarne la causa radice.
Un’ulteriore differenza di non poco conto tra la fault tree analysis e il modello FMEA, consiste nel fatto che mentre l’FTA prende in considerazione un asset specifico, come un impianto, l’FMEA si contraddistingue per effettuare un’analisi globale.
Come fare una FMEA?
Un’analisi FMEA inizia raccogliendo tutte le informazioni che abbiamo a proposito di un asset o di un processo. In manutenzione, è molto importante coinvolgere non solo le figure preposte a questa funzione, ma anche i responsabili della produzione, in modo da mettere insieme quante più idee possibili su come possa verificarsi un guasto.
Chiaramente, disporre di un’anagrafica tecnica completa e accurata ti permette di velocizzare il lavoro.
Raccolte queste informazioni, devono essere valutati tutti i possibili effetti che questi guasti potrebbero avere sul processo o sul sistema. Infine, deve essere valutata la gravità di questi effetti, che può essere poi collocata in una matrice a formare una scala ponderata dell’indice di gravità.
Assegnando un diverso peso a ciascuna tipologia o modalità di guasto, l’FMEA diventa a tutti gli effetti un criterio decisionale oggettivo per riuscire a prioritizzare gli interventi o svolgere manutenzioni preventive mirate a ridurre eventuali rischi.
Gli obiettivi FMEA.
I principali obiettivi di una FMEA sono:
- Migliorare la sicurezza
- Migliorare l’affidabilità degli asset (in termini di disponibilità)
- Ridurre i costi
- Supporto oggettivo nell’individuazione dei guasti e dei rischi
- Stabilire le priorità con cui effettuare gli interventi
- Migliorare le attività di prevenzione
Come applicare una FMEA in 7 step
Come si fa una FMEA? Per prima cosa, diciamo subito che in genere è sufficiente un foglio excel per svolgere un’analisi FMEA. Se disponi di un CMMS tanto meglio, molti software manutenzione contengono infatti un modulo dedicato all’analisi delle cause di guasto che può esserti molto utile sia in fase di brainstorming che in un momento successivo per continuare a monitorare e tenere aggiornata l’analisi.
Prima di entrare nel dettaglio di ciascuno di essi, vediamo rapidamente quali sono gli step necessari all’analisi FMEA.
- Identificare il componente, l’impianto o il processo che vogliamo analizzare
- Scomporre l’impianto in componenti o il processo in fasi e sottofasi (può essere utile aiutarsi con un diagramma di flusso)
- Identificare le potenziali modalità di guasto
- Identificare le possibili cause di guasto
- Per ciascuna modalità di guasto individuata, identificarne gli effetti
- Stabilire i criteri per la valutazione del rischio di ciascuna modalità di guasto e dei loro effetti. Questa valutazione deve includere la probabilità di occorrenza, la rilevabilità e la gravità del guasto
- Calcolare l’RPN (Risk Priority Number) e assegnare le priorità in base alla valutazione del rischio
- Eseguire le azioni necessarie ad eliminare o ridurre i rischi identificati tramite azioni preventive
- Misurazione del successo della riduzione del rischio
Le fasi dell’FMEA linee guida
Le fasi applicative dell’FMEA sono 5
- Fase preliminare: in cui si analizzano i componenti o i processi che vogliamo studiare
- Fase qualitativa: in cui si analizzano le modalità e le cause di guasto
- Fase quantitativa: in cui si definiscono gli indici di rischio e le priorità di intervento
- Fase correttiva: in cui si definiscono le azioni rivolte a ridurre il rischio
- Fase di misurazione: in cui si valutano le azioni intraprese
FMEA: la guida step by step
1. Analisi iniziale.
La fase di analisi iniziale viene svolta come un’analisi as-is (così com’è) del prodotto o del processo. A seconda che si intenda analizzare l’uno o l’altro, per questa attività possono tornare utili alcuni tool come una flow chart (un diagramma di flusso), QFD (Quality Funtion Deployment), alberi di guasto o VRP (Variety Reduction Program). Oltre a questi, se si tratta di un prodotto, come per esempio un impianto, può tornare utile disporre di un esploso della macchina per avere una visione completa dei componenti.
2. Individuare le modalità di guasto (Failure Mode Analysis)
Il secondo punto riguarda l’individuazione di tutte le possibili modalità di guasto (o di errore, se si tratta di processi o servizi). Le modalità di guasto descrivono tutti i modi in cui un oggetto può rompersi.
Molte aziende collocano all’interno di questa fase anche la ricerca delle cause di guasto (quindi un ulteriore step da effettuare in aggiunta all’individuazione delle modalità di guasto). Altre preferiscono inserire questa attività più avanti, dopo l’analisi degli effetti e la valutazione del rischio, in modo da concentrarsi solamente sugli asset più critici.
Questa attività è particolarmente utile quando si parla di manutenzione. Questo perché l’analisi delle modalità e delle cause di guasto può essere una risorsa utile in fase di pianificazione, aiutando il responsabile a costruire piani di manutenzione più accurati o inserire piccoli accorgimenti come check-list da associare a specifici ordini di lavoro o particolari asset.
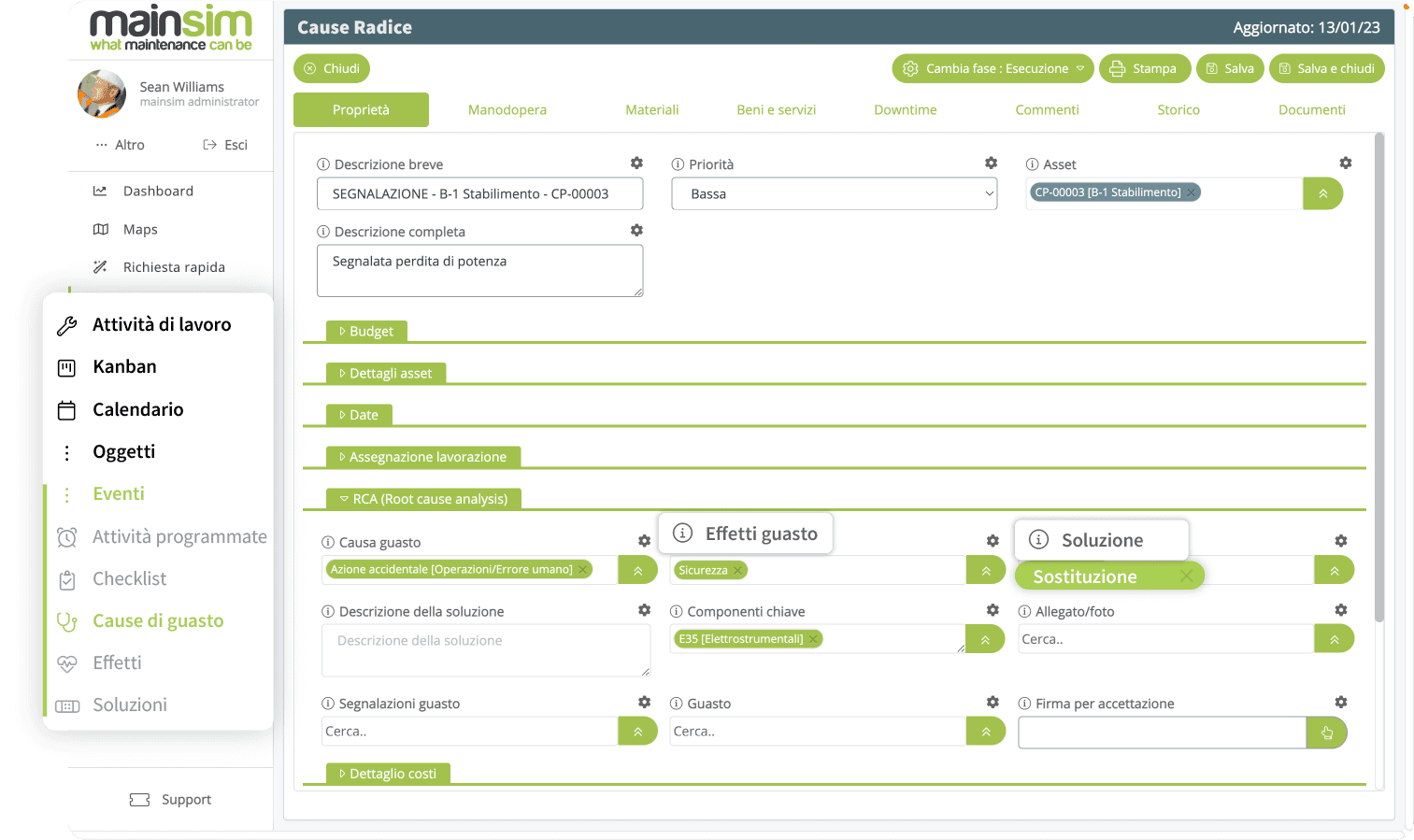
Le modalità di guasto possono essere poi raggruppate in diverse categorie che, in base al tipo di guasto che si verifica, ci permettano di stabilire il livello di criticità del guasto stesso. Un esempio di come strutturare queste categorie può essere:
- Malfunzionamento completo
- Riduzione delle prestazioni
- Guasto parziale
- Guasto intermittente
- Guasto non pregiudicante le funzioni
Quando si esegue una FMEA su attrezzature fisiche come per esempio un impianto anziché su un processo, le modalità di guasto diventano più specifiche.
Se prendiamo ad esempio il caso di una pompa centrifuga, tra le modalità di guasto troverò senz’altro guasti idraulici, meccanici, corrosione, intervento umano etc.
Se hai a disposizione l’esploso dell’impianto, puoi aiutarti con quello per individuare più facilmente le modalità di guasto possibili per ciascun componente che costituisce l’impianto.
Per quanto riguarda le cause di guasto, invece, è buona norma quella di suddividerle in macro-categorie, al cui interno andremo poi ad inserire le cause. Per esempio, potremmo creare una tabella con le seguenti macro-categorie:
Progettazione/costruzione/produzione
Errore di progettazione
Errore di fabbricazione
Errore di costruzione/installazione
Errore di modifica della progettazione
Ambiente esterno
Fuoco/fumo
Umidità
Alta/bassa temperatura
Campo elettromagnetico
Radiazione
Bio-organismi
Contaminazione/polvere/sporco
Operazioni/Errore umano
Azione accidentale
Procedura inadeguata/errata
Mancata esecuzione della procedura
Mancanza o assenza di formazione
Manutenzione inadeguata
Componente interno
Usura normale
Guasto precoce
Ambiente interno
Componente esterno
Sistemi di supporto
Connessioni
3. Individuare gli effetti
Per ciascuna modalità di guasto individuata, dovremo adesso identificare quali sono gli effetti che essa comporta sul nostro processo.
Alcuni esempi tra i più comuni possono essere:
- Nessun effetto
- impatto ambientale
- fermo macchina
- stallo
- perdita di automazione
- tempi di ciclo più lunghi rispetto a quelli nominali (perdita di quantità)
- ripartenze difficoltose dopo uno stop dovuto per esempio ad un intervento tecnico
- produzione di materiale non conforme (perdita di qualità)
- consumo eccessivo di materiali
- consumo eccessivo di corrente elettrica
- Sicurezza
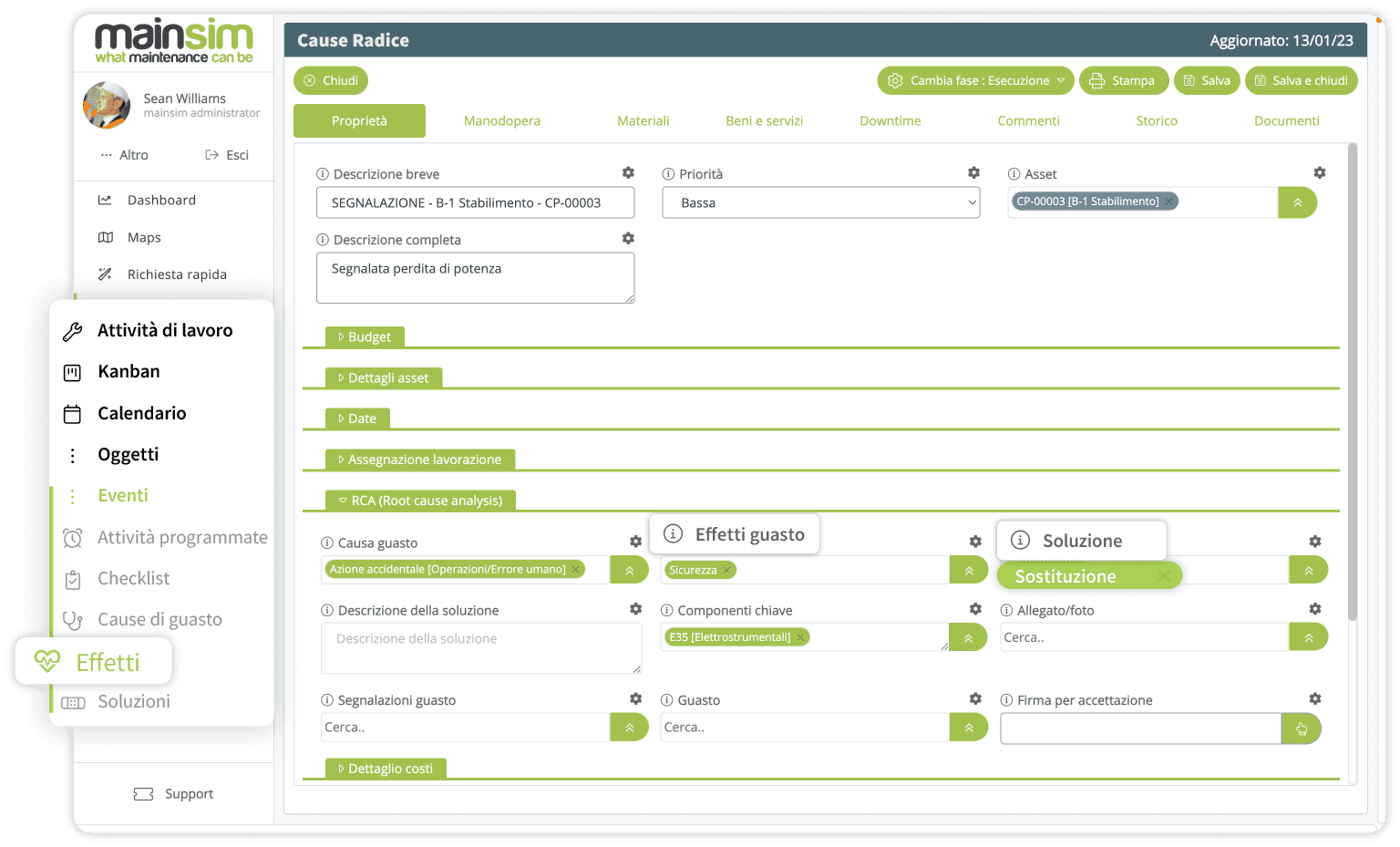
Se pensiamo a tutti gli effetti che un guasto può generare, sono davvero moltissimi. Per questo è buona norma suddividerli in base a dove essi si ripercuotono, un po’ come abbiamo fatto con le cause di guasto.
Un guasto può generare un effetto localizzato, come per esempio l’effetto di un componente difettoso.
L’effetto può però avere anche un impatto sul sottosistema su cui influisce. Una pompa centrifuga rotta, potrebbe per esempio avere un effetto sul sistema di raffreddamento a cui appartiene.
Ma l’effetto può anche avere ripercussioni sull’intero sistema. Continuando l’esempio qui sopra, l’effetto finale di un sistema di raffreddamento compromesso potrebbe avere come conseguenza un rallentamento dei livelli di produzione se non un arresto completo delle operazioni.
Una volta che siamo riusciti a mappare le modalità di guasto e gli effetti che generano sul nostro processo, possiamo provare a valutare il rischio che ognuno degli scenari descritti si verifichi, proseguendo con il passaggio successivo nella stesura della nostra analisi FMEA.
4. Valutazione dei rischi: FMECA e RPN
Abbiamo mappato tutte le possibili modalità di guasto e i rispettivi effetti che si ripercuotono sul processo. A questo punto è necessario riuscire a costruire una strategia per gestire ogni possibile scenario che abbiamo descritto.
Questi scenari però non avranno tutti la stessa gravità, la stessa probabilità di verificarsi e nemmeno la stessa probabilità di essere rilevati.
Il prossimo passo da compiere nella stesura nella nostra analisi FMEA/FMECA, riguarda la valutazione del rischio che ciascuno di questi eventi di cui sopra, accada.
Per la valutazione del rischio è importante riuscire ad ordinare i vari scenari in base alla gravità della situazione, in modo da avere un’idea oggettiva di ciò che richiede più urgentemente il nostro intervento.
Esiste uno strumento specifico da utilizzare e si tratta di una matrice all’interno della quale andiamo ad inserire i nostri scenari attribuendo loro un numero indice. Questo numero è frutto di un semplice calcolo ed è chiamato Risk Priority Number (RPN) che ci permette di creare una scala attraverso cui quantificare e ordinare il rischio generato da un evento.
Va da sé che più è alto il nostro RPN, più è alto il rischio generato dal guasto e dovremo quindi dare la priorità alle azioni specifiche tese a limitarne gli effetti e le conseguenze.
Il nostro scopo è dunque quello di costruire una scala di priorità popolata da numeri indice.
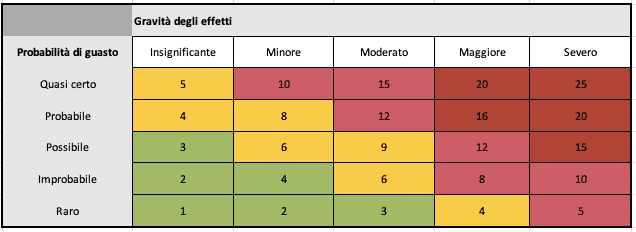
Il Risk Priority Number (RPN) è composto da 3 fattori che sono:
- Occorrenza (Occurrence – intesa come probabilità di guasto)
- Rilevabilità (Detection – intesa come capacità di rilevare il guasto)
- Gravità (Severity – intesa come la gravità degli effetti generati dal guasto)
Probabillità di guasto (Occurrence)
La probabilità di guasto (o di fallimento) indica con quale probabilità un’apparecchiatura, un componente o un sistema si guasti. Il nostro scopo qui è quello di attribuire un numero indice a questa probabilità per ogni modalità di guasto che abbiamo individuato. Un punteggio più alto significherà che la probabilità di guasto è molto alta e che l’evento si verificherà quasi certamente. Al contrario, un valore basso indica che il tipo guasto è molto raro.
Ovviamente, quando valutiamo le probabilità che si verifichi un guasto dovremmo tenere conto di diversi fattori, come la vetustità del bene o eventuali fluttuazioni stagionali dei guasti.
Il contributo maggiore in questo caso lo danno i dati storici in nostro possesso. Se possiedi un CMMS o un altro software manutenzione, sarà senz’altro una fonte inesauribile di dati dai quali puoi ricavare informazioni molto preziose per rendere più accurate le tue valutazioni.
Ovviamente anche l’esperienza degli addetti alla manutenzione o dei responsabili di produzione rappresenta una fonte grande valore.
Ci sono infine delle metriche specifiche che possono aiutarci a stabilire la probabliltà di guasto. Le due più importanti che meritano di essere segnalate sono:
- Failure Rate
- MTBF (Mean Time To Failure)
Il failure rate indica il rapporto tra numero di cicli produttivi e il quelli complessivi.
Il MTBF rappresenta invece il tempo medio tra i guasti ed è senza dubbio una delle metriche più utilizzate in manutenzione. Conoscendo il mean time between failure, avremo infatti una misura statistica dell’occorrenza di un guasto su un determinato impianto, permettendoci di stabilire con più precisione l’occorrenza.
Se utilizzi un buon CMMS (Computerized Maintenance Management System) o un EAM (Enterprise Asset Management), molto probabilmente disporrai già di questa metrica. In realtà non tutti i CMMS o gli EAM sono in grado di calcolare il MTBF, ma e1 una funzione molto utile e non soltanto nel caso di un’analisi FMEA, ma anche per costruire piani di manutenzione migliori e prevenire i guasti (che è comunque uno degli obiettivi che ci siamo posti nel momento in cui abbiamo deciso di effettuare un’analisi con il modello FMEA/FMECA).
Messi insieme i pezzi, andiamo a comporre la nostra scala, che generalmente si presenta come la seguente:
- 1 – Evento estremamente improbabile.
- da 2 a 4 – L’evento può verificarsi in alcuni casi, ma c’è solo una minima probabilità che accada.
- da 5 a 7 – L’evento può verificarsi occasionalmente.
- da 8 a 9 – Esiste una alta probabilità che si verifichi l’evento.
- 10 – L’evento è inevitabile.
Rilevabilità del guasto (Detection)
Il secondo valore di cui abbiamo bisogno è l’indice di rilevabilità di un guasto. Si tratta quindi della nostra capacità di diagnosticare il verificarsi di uno di questi effetti generati da un guasto.
Per ogni effetto descritto, dobbiamo quindi attribuire un valore che rappresenta questa capacità.
Ancora una volta, possiamo servirci di una scala da 1 a 10. Più è alto il valore, più è probabile che l’evento non venga intercettato. Per cui ad eventi di guasto facilmente intercettabili, viene assegnato un punteggio basso.
Per riuscire ad abbassare la rilevabilità del guasto (e quindi migliorare la nostra capacità di rilevazione del guasto) le aziende possono avvalersi di sensori di controllo applicati agli asset, letture di contatori, telecamere, azioni di manutenzione preventiva o ancora meglio ispezioni regolari che ci permettano di monitorare con frequenza i nostri impianti.
Ad esempio, se installiamo dei sensori su di un sistema HVAC, l’indice di rilevabilità sarà inevitabilmente più basso.
Gravità del guasto (Severity)
L’ultimo fattore da considerare per il calcolo del Risk Priority Number (RPN) è la c.d. Severity, cioè la gravità degli effetti generati dal guasto. Questa valutazione ci porta infatti a cercare di quantificare la gravità di un evento e di una serie di effetti ad esso correlati. Per ogni modalità di guasto (failure mode) dobbiamo quantificarne la gravità.
Anche in questo caso utilizziamo una scala da 1 a 10, in cui come al solito 1 indica il livello di gravità più basso.
Ovviamente, rispetto per esempio all’analisi dell’occorrenza di un guasto per stabilire la quale possiamo (e dobbiamo!) avvalerci di dati storici, la valutazione della gravità ha una natura più soggettiva, per cui solitamente si tende a stabilire un criterio valido deciso dall’azienda. Potremmo decidere infatti di basare la valutazione sulle implicazioni monetarie scaturite da un fermo macchina, o la riduzione in termini di produzione.
Allo stesso tempo però ci sono criteri che dovrebbero essere fondamentali per chiunque, come il rischio per la sicurezza o per l’impatto ambientale. Generalmente infatti si stabilisce un indice di gravità pari a 9 o 10 se gli effetti di un guasto hanno implicazioni in materia di sicurezza. Un valore di 7-8 indica invece una situazione critica.
Come calcolare l’RPN (Risk Priority Number) per l’FMEA
Abbiamo visto cos’è l’RPN (Risk Priority Number) e da cosa è composto. Aggiungo soltanto che in italiano si trova spesso sotto un altro acronimo che è quello di IPR, e cioè Indice di Priorità di Rischio. Altre volte ancora si parla invece di Indice di Criticità (espresso talvolta con la lettera C), ma stiamo parlando sempre della stessa cosa.
Questo RPN o se vogliamo IPR, non è altro che un indicatore che ci permette di stabilire le priorità per le nostre differenti modalità di guasto che abbiamo descritto nell’FMEA o nell’FMECA. L’obiettivo è quello di aiutarci a stabilire quando è effettivamente il caso di intervenire e quando invece il rischio che un evento si verifichi è accettabile al punto da poter rimandare o posticipare il nostro intervento.
Ma come calcolare l’RPN o IPR?
È molto semplice. O almeno lo sarà una volta stabiliti i nostri indici per la probabilità di guasto (occorrenza), rilevabilità e gravità.
Questi tre fattori sono di solito indicati con la prima lettera della parola in inglese. Quindi:
- Occurrence (O)
- Detection (D)
- Severity (S)
Siccome talvolta tra italiano e inglese si tende a fare una gran confusione, ecco gli stessi nomi per IPR, la versione italiana dell’RPN:
- Occorrenza (O), spesso indicata anche come Probabilità (P)
- Rilevabilità (R)
- Gravità (G)
Dopo che avremo assegnato per ciascuno di questi fattori un numero indice su una scala da 1 a 10 come abbiamo visto nel paragrafo precedente, e avremo fatto lo stesso per ciascuna modalità di guasto, per alcolare il rispettivo RPN (l’indice di priorità di rischio) è sufficiente moltiplicare questi 3 fattori. Quindi:
RPN = Occurence x Detection x Severity
oppure, se preferite:
IPR = O x R x G
In cocnlusione, ill numero di priorità di rischio (RPN) è il prodotto finale che ci consente di classificare la criticità di ogni asset. Compilando la nostra scheda FMEA, avremo come risultato una matrice che ci permette a colpo d’occhio di classificare i vari guasti in base alla loro criticità e dunque al rischio che essi comportano sul nostro processo.
FMEA esempi
Il modo migliore e più economico per effettuare un’analisi FMEA è forse quello di aiutarsi con un foglio excel.
Di seguito troverai un esempio di modello FMEA excel. È solo una bozza, ma dovrebbe servirti per capire come impostare questo tipo di analisi in base ai tuoi asset, al tuo processo o al tuo prodotto.
In questo articolo abbiamo precedentemente preso come esempio una pompa centrifuga, per cui continuerei con questa.
FMEA fasi:
Per prima cosa abbiamo analizzato la pompa, i componenti da cui è composta e tutto ciò che in qualche modo è legata ad essa, compresi i processi produttivi per i quali il funzionamento della pompa si rende necessario.
Dopo l’analisi, abbiamo valutato quali sono i tipi di guasto che possono accadere, descrivendo i vari scenari e individuando le possibili cause. Ovviamente non ci siamo limitati alla rottura di uno dei componenti, ma abbiamo preso in esame anche l’ambiente esterno in cui la pompa si trova a lavorare.
Analizzate le possibili modalità di guasto, abbiamo proseguito l’analisi FMEA/FMECA andando a descrivere quali sono i possibili effetti generati da ciascuna tipologia di guasto che abbiamo individuato. Abbiamo analizzato gli effetti a livello locale, a livello di sistema e di processo, mappandoli su di un foglio excel.
A questo punto non resta che costruire la matrice di valutazione del rischio calcolando l’RPN per ciascuna modalità di guasto individuata. Per farlo abbiamo bisogno di tre fattori: il primo è la probabilità che questo guasto si verifichi, per cui abbiamo messo insieme la nostra esperienza e i dati di cui siamo in possesso per stabilire un numero indice su una scala da 1 a 10 per ciascuna tipologia di guasto. Questa è la nostra tabella delle occorrenze FMEA.
Il secondo fattore riguarda la nostra capacità effettiva di rilevare il guasto. Ci sono dei sensori che possono indicarci quando la pompa non sta funzionando nel modo corretto? Abbiamo qualche altro meccanismo che ci permette di rendercene conto? Attribuiamo anche in questo caso un numero indice su una scala da 1 a 10.
Lo stesso facciamo per la gravità. Stabilire la gravità di ciascun guasto può essere complesso per cui è importante stabilire quali sono i moventi che ci fanno percepire un guasto come più grave di un altro, tenendo sempre presente che la sicurezza viene sempre prima di tutto.
Infine, calcolo l’RPN (o IPR – indice di priorità di rischio, in italiano) moltiplicando tra loro questi tre fattori. Riporto i valori all’interno delle appostie caselle del mio foglio excel e il gioco è fatto.
Alcuni consigli per il modello excel: come compilare una FMEA?
Strutturare un’analisi FMEA/FMECA in excel è piuttosto semplice. È buona norma però seguire alcune linee guida.
L’intestazione del modello FMEA dovrebbe includere almeno i seguenti campi:
- Prodotto/parte: nome o numero identificativo del prodotto
- Team: elenco dei nomi di chi ha partecipato all’analsi FMEA
- Numero FMEA: il numero di controllo del documento
- Data
- Data di revisione
Colonne:
- Processo
- Funzione del processo
- Requisiti
- Modalità di guasto
- Causa di guasto
- Effetti
- Gravità (S)
- Occorrenza (O)
- Rilevabilità (D)
- Metodo di controllo: specificare il metodo di controllo previsto per rilevare il guasto
- RPN
- Azione consigliata
- Responsabile: la singola persona o il team responsabile per il tipo di guasto o per l’asset
- Data di fine obiettivo: indica la data di completamente del piano
Scarica il modello FMEA excel in italiano.
Vantaggi FMEA
Al giorno d’oggi la FMEA come l’FMECA sono applicati nei più disparati settori, da quello manifatturiero all’healthcare e la sanità, e non più soltanto all’automotive o al settore aeronautico e quello spaziale. Ciò perché il modello si è confermato nel tempo come molto valido e anche raccomandato dalle norme UNI e ISO per la valutazione dei rischi, oltre che dalla metodologia Six Sigma. Infine, i vantaggi di un’analisi FMEA per la manutenzione sono a dir poco enormi sia in ambito produttivo che nel facility management.
Tra i principali vantaggi della compilazione di un modello FMEA o FMECA sono contemplati:
- Individuazione preventiva delle potenziali modalità di guasto
- Determinazione delle cause di guasto ordinate dalle più frequenti alle meno frequenti
- Valutazione degli effetti che ciascuna tipologia di guasto implica sul sistema
- Quantificare gli indici di rischio in modo da poter stabilire un sistema di priorità oggettivo per gli interventi da effettuare
- Eliminazione o riduzione delle cause radice di guasto in modo complementare alla Root Cause Analysis (RCA)
- Identificare quali sono gli interventi di manutenzione correttiva e quelli di manutenzione preventiva
- Costruire piani di manutenzione più efficaci
- Mappare le criticità in modo ordinato e facilmente consultabile
Unisciti agli esperti
Oppure scopri il CMMS mainsim in meno di 3 minuti con questo video.
Ricevi i migliori consigli di manutenzione una volta al mese.
Unisciti agli esperti di manutenzione. Ricevi nuove risorse una volta al mese direttamente nella tua casella e-mail. E puoi annullare l’iscrizione quando vuoi.