Analisi RAMS
Cos’è, come e perché fare un’analisi RAMS
RAMS: Reliability, Availability, Maintenability, Safety.
Al giorno d’oggi, la crescente complessità dei sistemi industriali e degli impianti produttivi, unita ad una maggiore richiesta di affidabilità dei tempi di consegna dei prodotti e una sempre maggiore competizione sul mercato, implica per le aziende la necessità di ridurre al minimo le interruzioni e i fermi macchina imprevisti.
L’analisi RAMS permette di valutare i parametri di affidabilità, disponibilità, manutenibilità e sicurezza delle proprie apparecchiature, aiutando le aziende ad individuare eventuali punti deboli e colli di bottiglia, per predisporre le contromisure necessarie e valutare le opportune modifiche.
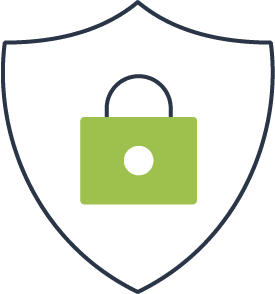
Definizione di RAMS: cos’è e cosa significa?
RAMS è l’acronimo dei termini inglesi Reliability, Availability, Maintenability e Safety.
Questi termini, con cui qualunque ingegnere della manutenzione dovrebbe essere familiare, sono traducibili in italiano con:
- Affidabilità (Reliability)
- Disponibilità (Availability)
- Manutenibilità (Maintenability)
- Sicurezza (Safety)
L’analisi RAMS è dunque una disciplina propria dell’ingegneria della produzione e della manutenzione.
Le discipline RAMS si compongono di un insieme di metodi e di strumenti di analisi che permettono di valutare le condizioni di affidabilità, disponibilità, manutenibilità e sicurezza dei propri impianti e processi, con l’obiettivo finale di garantire e massimizzare il corretto funzionamento di tali sistemi in un contesto produttivo, ottimizzando tempi e costi di produzione.
I risultati dell’analisi RAMS (alla quale spesso ci si riferisce anche con l’acronimo RAM), forniscono informazioni utili al miglioramento della gestione della manutenzione dei propri impianti e dei sistemi produttivi.
In altre parole, permettono di ottimizzare la gestione dei nostri asset, migliorandone la loro disponibilità e permettendoci di ridurre i fermi macchina inaspettati o imprevisti cali di produzione.
RAMS: cenni storici
L’interesse ingegneristico verso le metodologie di analisi RAMS iniziano ad emergere durante il secondo conflitto mondiale. Nel periodo post-bellico, l’approccio RAMS alla produzione subisce un forte impulso dovuto principalmente all’emergere di nuove tecnologie in campo militare, aeronautico e spaziale.
Successivamente, sulla spinta dei successi ottenuti negli Stati Uniti, lo stesso approccio RAMS si trasferisce dal settore militare a quello civile e all’impiantistica di produzione, divenendo uno standard in ambito industriale.
Obiettivi della RAMS
L’obiettivo di un’analisi RAMS è quello di individuare, fin dalle fasi di sviluppo di un prodotto, quali sono le criticità dei nostri impianti e sistemi, in modo tale da correggere gli errori ed evitare fermi macchina che non sono stati pianificati (quindi tutti quelli che avvengono al di fuori delle nostre politiche di manutenzione preventiva) o perdite di produzione durante la fase di operation.
In altri termini, un’analisi RAMS ben fatta ci permette di identificare preventivamente le soluzioni opportune a ridurre i guasti e migliorare la gestione delle nostre risorse.
Gli obiettivi sono dunque:
- massimizzare l’affidabilità e la disponibilità dei nostri impianti
- ottimizzare la manutenzione
- perfezionare la gestione delle scorte e dei materiali di ricambio
- valutare i rischi generati da un errore o un fermo macchina
- correggere le criticità
- migliorare la sicurezza
- stabilire le nostre priorità
- evitare perdite di produzione
RAMS: Reliability, availability, maintenibility and safety.
Prima di esplorare nel dettaglio quali sono gli strumenti che possiamo utilizzare per effettuare un’analisi RAMS dei nostri impianti, macchinari, sistemi e processi, vediamo velocemente cosa significano i termini affidabilità, disponibilità, manutenibilità e sicurezza da un punto di vista ingegneristico.
L’approccio RAMS allo studio dei nostri macchinari mutua gli strumenti di analisi che derivano da altre metodologie e approcci che sono connessi alla manutenzione degli impianti, quali:
Affidabilità (Reliability)
L’affidabilità di un impianto o di un sistema (in inglese reliability) indica la probabilità che lo stesso subisca un guasto.
Si definisce affidabilità di un componente, un impianto o un sistema la probabilità che esso non incorra in alcun guasto per un certo periodo di tempo (t).
L’affidabilità, solitamente indicata con la lettera R, è strettamente correlata al tasso di guasto.
Il tasso di guasto è un indicatore che ci aiuta a determinare, statisticamente, il numero di guasti in cui un componente può incorrere in un determinato tempo (t).
Conoscere il tasso di guasto di un nostro impianto, ci permette dunque di determinare l’affidabilità dello stesso, individuare le criticità e stabilire opportune politiche di manutenzione per aumentarne l’affidabilità (e la disponibilità).
Simile alla Disponibilità, l’affidabilità di un impianto è difficile da misurare. Essendo strettamente correlata alla probabilità di guasto, esistono diversi modi per calcolarla. Il più comune è consiste nel calcolare il tempo medio tra i guasti (MTBF).
Disponibilità (Disponibility)
Dato un tempo t, la disponibilità (Availability) è definita come la percentuale di esso in cui un impianto o un macchinario rimane operativo in circostanze normali per servire lo scopo previsto.
La formula matematica per il calcolo della disponibilità è la seguente:
% di disponibilità = (tempo trascorso totale – somma dei tempi di fermo)/tempo trascorso totale
Manutenibilità (Maintenability)
La manutenibilità di un impianto o di un componente (maintenability) è definita come la probabilità di eseguire con successo un’azione di riparazione entro un determinato tempo.
Anch’essa simile all’affidabilità, in questo caso la variabile di interesse è però il tempo t di riparazione, piuttosto che il tempo di guasto.
Sebbene ci siano molti modi per calcolare la manutenibilità, il modo più comune è quello di calcolare il tempo medio necessario per riparare un’attrezzatura. Si tratta del tempo medio di riparazione (MTR), noto anche come MTTR (Mean Time To Repair).
MTR = Tempo di inattività totale (ore) / Numero di eventi di guasto
Sicurezza (Safety)
La sicurezza (safety) di un impianto, di un sistema o di un processo è definita come la probabilità di accadimento di un evento potenzialmente pericoloso per l’ambiente o per le persone.
Esistono diverse tecniche che ci aiutano nell’analisi dei rischi, con l’obiettivo di valutarne e mitigarne il più possibile gli effetti ed eliminare le criticità.
Quali sono allora i vantaggi derivanti da un’analisi RAM?
Adesso che abbiamo visto più nel particolare gli indicatori che compongono la RAM (per il momento escludiamo la S di safety), ci sarà più facile comprendere lo scopo dell’analisi:
“L’obiettivo è quello di garantire la massima disponibilità del nostro impianto, individuando quali sono gli elementi più critici e che presentano un maggior rischio di compromettere la produzione a causa di tassi di guasto più elevati o tempi di riparazione più lunghi, compromettendone anche la sicurezza e incidendo sui costi e i livelli di produzione.”
Come si fa un’analisi RAMS?
Scomposta la RAMS nei quattro componenti che ne compongono l’acronimo, passiamo a parlare degli strumenti per monitorare, misurare e valutare i singoli fattori.
*Abbiamo parlato in modo più approfondito dei singoli strumenti riportati di seguito in vari articoli. Per cui, se vuoi approfondirne qualcuno in particolare, clicca sui link che trovi nel testo per un maggiore dettaglio.
Esistono molti metodi e strumenti che ci aiutano a studiare l’affidabilità e la disponibilità dei nostri impianti, sistemi e processi.
- FMEA e FMECA → analisi modalità di guasto, analisi degli effetti e soluzioni
- Fault Tree Analysis (FTA) – Albero dei guasti → probabilità di guasto
- Reliability Block Diagram → calcolo dell’affidabilità e della disponibilità complessive di un sistema
- Tasso di guasto → probabilità del verificarsi di un guasto
- Analisi dei guasti e root cause analysis (RCA) → Analisi delle cause che portano al generarsi di un guasto
Tecniche e strumenti per l’analisi dei rischi legati alla sicurezza:
- Hazop (Hazard and operability analysis)
- LOPA (Layer of protection analysis)
- PHA (Process hazard analysis)
Esistono poi molti indicatori e metriche che ci aiutano a calcolare i vari fattori che compongono la RAMS. I principali sono:
- MTBF – mean time between failure (Tempo medio tra i guasti)
- MTTR – mean time to repair (tempo medio di riparazione)
- MTTF – mean time to failure (tempo medio al verificarsi di un guasto)
- MDT – mean down time (tempo medio di fermo macchina)
- MTBM – mean time between maintenance (tempo medio tra le manutenzioni)
Affidabilità e disponibilità nell’analisi RAMS
I risultati di un’analisi RAM forniscono informazioni particolarmente utili per migliorare i piani di manutenzione dei nostri impianti, aiutandoci ad individuare i punti deboli delle nostre strutture.
Affidabilità e disponibilità (le prime due lettere dell’acronimo RAMS) possono essere valutate in modo probabilistico utilizzando sia delle vere e proprie tecniche di analisi che degli indicatori.
1. RAMS: FMECA e FMEA (Failure Mode and Effects Analysis)
L’analisi FMEA ci permette di analizzare in modo approfondito le modalità di guasto (failure mode) dei nostri impianti e macchinari, determinando gli effetti che essi possono generare sul sistema.
L’analisi FMECA è in sostanza un’evoluzione della stessa FMEA, introducendo però un metodo per stabilire le priorità tramite la valutazione del rischio. Il risk priority number (RPN) ci permette infatti di associare a ciascuna tipologia di guasto un numero indice in base alla gravità degli effetti generati sul sistema dal guasto stesso.
L’FMECA diviene dunque la base da cui partire per ottenere una visione globale delle varie tipologie di guasto delle nostre macchine, insieme alla loro frequenza e la gravità (severity) degli stessi.
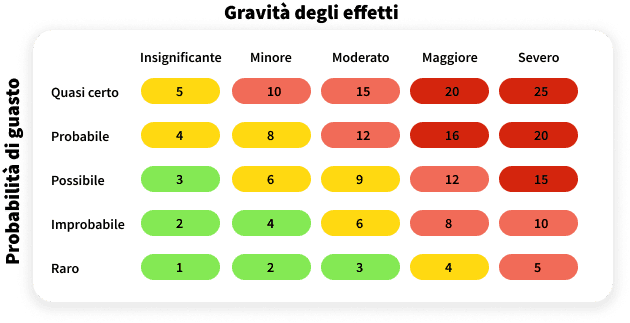
2. RAMS: Fault Tree Analiysis (FTA) – albero dei guasti
La fault tree analysis (FTA – in italiano albero dei guasti), ci permette di studiare le cause dei guasti, identificando quali sono gli eventi base che condurranno ad un guasto maggiore (top event). Tali eventi sono classificabili in:
- guasti primari
- guasti intermedi
- guasti secondari
Attraverso una rappresentazione ad albero dell’impianto in esame, o una parte di esso, ci consente di evidenziare quali sono le interconnessioni fisiche e logiche tra i vari componenti che lo costituiscono. Il fine è quindi quello di individuare le connessioni strutturali che hanno per esempio portato da un guasto minore ad uno di entità maggiore.
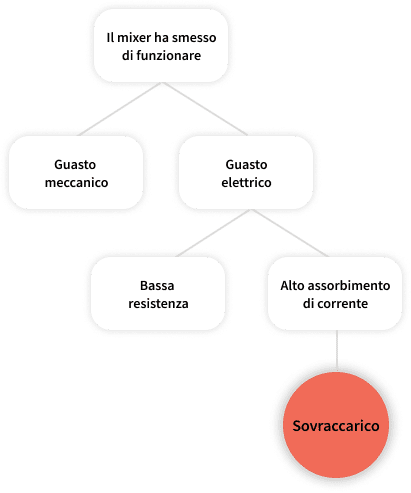
3. RAMS: Reliability Block Diagram (RBD)
Un ulteriore strumento utile per lo studio RAMS, è il così detto reliability block diagram (RBD).
Questo tipo di analisi è costituita da un diagramma a blocchi che, come nella fault tree analysis, ci permette di rappresentare un impianto come una rete logica complessa, composta da blocchi messi in relazione tra loro tramite nodi. Ogni blocco rappresenta un componente del sistema.
Scomposto in questo modo l’impianto in blocchi o sotto-sistemi, e attribuendo a ciascuno di loro un indice di affidabilità, ci permette di calcolare l’affidabilità complessiva dell’impianto a partire dai valori attribuiti ai singoli elementi.
La manutenibilità nello studio RAMS
Abbiamo definito la manutenibilità come la probabilità che un macchinario o un suo componente sia riparato in un intervallo di tempo prestabilito, considerando l’intero processo di manutenzione, quindi dalla rilevazione del guasto fino al ripristino dell’impianto.
L’analisi di manutenibilità (la terza lettera dell’acronimo RAMS) stima quindi il tempo totale di inattività per ciascuna modalità di guasto possibile di un impianto o di un sistema.
L’indicatore principale attraverso cui possiamo analizzare la manutenibilità di un nostro macchinario è dunque il tempo medio di riparazione (MTTR – mean time to repair).
La sicurezza nell’approccio RAMS
L’ultima lettera dell’acronimo RAMS, ma non in ordine di importanza, è riferita al tema della sicurezza (safety) per l’ambiente e le persone coinvolte nella conduzione dei nostri impianti.
Oltre a tenere conto delle prescrizioni legislative in tema di sicurezza, tra le principali tecniche di analisi dei rischi, meritano di essere menzionate:
- HAZOP (Hazard and operability analysis): questa tecnica di analisi è basata sul lavoro di gruppo, mirato all’individuazione dei pericoli esistenti in un determinato processo produttivo o manutentivo.
- LOPA (Layer of protection analysis): questa tecnica di analisi e valutazione dei rischi ci permette di verificare l’efficacia delle misure di sicurezza che sono adottate all’interno di un’azienda, con l’obiettivo di comprendere quanti e quali sono i diversi livelli (layers) necessari a ridurre il rischio generato da un guasto o da un’anomalia.
- PHA (Process Hazard Analysis): spesso utilizzata in fase di progettazione, questo tipo di analisi permette al costruttore di individuare quali sono rischi pericoli legati ad un processo di produzione industriale, a partire dalle potenziali cause e conseguenze di guasti, eventi ambientali o errori umani.
Le fasi di un’analisi RAMS:
Quando si parla di analisi RAMS non si intende quindi un’analisi o uno strumento specifico, ma piuttosto una serie di analisi, strumenti e indicatori i quali, messi insieme, ci permettono di monitorare e valutare ciascuno degli aspetti che compongono la RAMS, dall’affidabilità fino alla sicurezza.
Inoltre, è importante sottolineare che, non essendo la RAMS una metodologia specifica, ma anzi un insieme di tecniche e strumenti differenti e separati tra loro, non esiste un processo unico e valido per tutti: potremmo infatti decidere di affidarci un tipo di analisi piuttosto che un’altra, oppure calcolare o meno un indicatore preciso.
Quello che possiamo fare però, è provare a comporre un possibile workflow di lavoro, strutturato in diverse fasi che toccano ciascuna i vari punti coinvolti nella RAMS.
- Censimento delle risorse: a prescindere da tutto, è fondamentale partire con il piede giusto. Per portare avanti un’analisi RAMS efficace, dovremo per prima cosa decidere quali macchine e impianti vorremo coinvolgere nell’analisi. Se disponi già di un’anagrafica dei tuoi asset, sei a cavallo!
- FMEA (o ancora meglio, FMECA): probabilmente un FMECA è l’analisi più importante ai fini di uno studio RAMS. Non è un processo veloce e nemmeno definitivo (per continuare ad essere valido deve anche essere reiterato nel tempo) ma ti permetterà di avere una panoramica più o meno completa di ciascuna modalità di guasto (failure mode, la F e la M dell’acronimo) identificando quindi i punti deboli di un’apparecchiatura o di un sistema, determinandone gli effetti sul processo e valutandone i rispettivi rischi. Attribuendo poi un indice di rischio (risk priority number – RPN) sarai in grado di stabilire le priorità di intervento e quali apparecchiature monitorare con maggiore frequenza e attenzione per evitare guasti inattesi. Questo tipo di analisi riguarda inoltre sia l’affidabilità che la disponibilità dei tuoi macchinari, quindi la R e la A dello studio RAMS (realibility e availability) ma anche la sicurezza (quindi vale davvero la pena!)
- Calcolo del Mean Time Between Failure: calcolare il MTBF di ciascun impianto coinvolto nello studio RAMS, avrai una stima (quindi una statistica) dell’occorrenza dei guasti, il tempo medio tra il verificarsi di un fermo e quello successivo. Un’informazione preziosa sia quando si parla di affidabilità di un sistema che della sua disponibilità.
- Reliability block diagram e FTA: per completare l’analisi di affidabilità, è una buona idea quella di aggiungere allo studio anche un RBD (reliability block diagram) e/o un’analisi dell’albero dei guasti (FTA – Fault Tree Analysis). Ciò ti permetterà di migliorare la conoscenza e comprensione dei tuoi impianti, stabilire quali sono le connessioni tra i vari sotto-sistemi e componenti, predisponendo piani di manutenzione ed ispezioni laddove ce n’è più bisogno.
- Identificazione delle apparecchiature critiche: mettendo insieme i dati generati dalle fasi precedenti, è possibile identificare e valutare meglio le criticità basate sull’occorrenza dei guasti e sull’impatto che essi hanno sull’intero sistema e sulla produzione.
- Analisi di manutenibilità: attraverso il calcolo del tempo medio di riparazione (MTTR) puoi avere una stima del tempo di inattività totale di un impianto per ciascuna modalità di guasto. Questo rappresenta un tassello importante di uno studio RAMS, permettendoti per esempio di decidere, sulla base dei dati, tra politiche di manutenzione preventiva o correttiva.
- Stima del carico di lavoro: a questo punto, dovresti essere in grado di stimare il carico di lavoro necessario alla tua squadra di manutenzione per le attività di ispezione regolari, quelle di manutenzione preventiva e di manutenzione correttiva. Se disponi di un CMMS, non dovrebbe essere molto difficile poiché avrai certamente la quantità (e la qualità!) dei dati necessaria ad un’attività di questo tipo.
- Analisi della sicurezza: se hai svolto l’analisi FMECA (o FMEA) descritta al punto 2, sei già un passo avanti. A questo punto non resta che metterti seduto insieme ai tuoi collaboratori, analizzare i processi di produzione e quelli manutentivi, cercando di individuare quali sono i potenziali rischi nella gestione degli asset attraverso le analisi di cui abbiamo parlato sopra.
- Analisi dei costi di gestione: giunto a questo punto, potrebbe essere una buona idea quella di analizzare in modo più approfondito quali sono i costi di gestione degli asset presi in considerazione durante lo studio RAMS. Farlo potrebbe non essere così semplice, almeno che tu, ancora una volta, non disponga di un CMMS, il quale ti permette di avere una panoramica completa degli aspetti economici legati all’asset management e al LCC (life cost cycle ) dell’impianto.
Cosa serve per fare l’analisi RAMS: dati e software
Per effettuare un’analisi RAMS la prima cosa di cui abbiamo bisogno sono i dati.
Senza avere a disposizione informazioni corrette e affidabili, non potremo analizzare l’affidabilità, la disponibilità e la manutenibilità dei nostri impianti e valutarne le prestazioni.
Detto questo, ci sono molti modi, e alcuni di questi anche estremamente economici, per riuscire a mettere insieme una banca dati decente.
Per esempio, possiamo creare uno registro degli interventi, una sorta di cronologia di tutti gli interventi tecnici effettuati su ciascuno dei nostri impianti, in modo poi da poterli analizzare. In questo modo potremmo raccogliere informazioni molto utili sull’affidabilità e la disponibilità degli impianti.
Se all’interno di questa cronologia aggiungiamo poi le date, oppure i tempi di intervento (per esempio mediante la compilazione di un rapportino di fine lavoro), la nostra analisi potrà spingersi anche più in là, includendo metriche e indicatori come il MTBF o il MTTR.
La maturità dell’azienda gioca ovviamente un ruolo fondamentale, e le metriche o i KPI che desidera monitorare vanno di pari passo con essa.
Ovviamente, il livello di digitalizzazione rappresenta un aspetto centrale nella nostra capacità di acquisire dati di qualità per la RAMS.
A seconda di quali dati ci interessi maggiormente raccogliere, abbiamo a disposizione diverse tipologie di software: dai sistemi MES (Manufacturing execution system) per il monitoraggio della produzione, a software manutenzione CMMS (Computerized Maintenance Management System) fino ai più semplici tool di field service management.
Inoltre, raccolti i dati, avremo bisogno anche di uno strumento di analisi che sia in grado di organizzare queste informazioni e renderle immediatamente comprensibili.
Chiaro che ci sono dei costi da sostenere e probabilmente dovremo fare delle scelte e trovare dei compromessi.
Perché scegliere un CMMS?
Un software CMMS ti permette di gestire i tuoi impianti e tutte le attività correlate alla manutenzione. Potrai raccogliere dati in modo automatico, gestire i tecnici sul campo attraverso l’app mobile, acquisire i dati che ti interessa monitorare e analizzarli attraverso il tool di BI integrato nella piattaforma.
Il sistema è progettato per restituire in modo automatico i principali indicatori di asset management, come MTBF o MTTR e permette di analizzare i guasti e le cause di guasto, semplificando la stesura di un’analisi FMEA. Inoltre, ti permetterà di gestire anche i processi di manutenzione, aiutandoti a migliorare l’affidabilità, la disponibilità e la manutenibilità dei tuoi impianti. Infine, per quanto riguarda la sicurezza, molti CMMS come mainsim, permettono anche di registrare i near miss (quasi infortuni), gestire la documentazione per la sicurezza di tecnici e fornitori, aggiungere check-list e molti strumenti, contribuendo alla gestione e alla valutazione dei rischi in ambito sicurezza.
Guarda uno dei video e scopri come mainsim può aiutarti a raccogliere e analizzare i dati che cerchi:
RAMS esempio:
L’esempio che proponiamo è quello di un’analisi RAMS nel settore ferroviario. Nonostante il settore ferroviario abbia da poco abbracciato i metodi di studio RAMS, in ambito europeo sono state varate alcune normative riguardanti questo settore, con particolare riguardo alla sicurezza e all’affidabilità (EN50126, EN50128 e EN50129).
Analisi RAMS durante il ciclo di vita del prodotto (LCC – Life Cycle Cost)
Prendiamo come esempio RAMS il ruolo dell’analisi lungo le diverse fasi di una commessa relativa alla fornitura di un impianto di bordo per un veicolo ferroviario. Si tratta quindi di un rapporto di fornitura tra azienda costruttrice (fornitore) ed il cliente che costruisce il veicolo.
Tra i requisiti richiesti nel bando di gara, vi saranno anche i requisiti RAMS, quindi di affidabilità, disponibilità, manutenibilità e sicurezza dell’impianto in questione.
Il costruttore del treno, il quale si rivolge al proprio fornitore per la realizzazione di vari sotto-sistemi, realizza un RBD (realibility block diagram) con l’intento di ripartire ed allocare i requisiti RAMS.
Il fornitore dovrà quindi dare prova del raggiungimento di tali requisiti.
Durante la fase di progettazione, ci si avvale di metodi tradizionalmente utilizzati per l’analisi RAMS come FMECA, Fault Tree Analysis (FTA) e Preliminary Hazard Analysis. In parallelo, viene portata avanti un’attenta analisi del costo di ciclo di vita del prodotto (Life Cycle Cost in modo da trovare un equilibrio tra il costo del prodotto e l’affidabilità dello stesso.
Analisi della sicurezza
L’analisi della sicurezza è connessa alla probabilità che si verifichi un guasto che esponga ad un rischio di sicurezza del treno. Questi possono esseri derivanti da un guasto o da un errore umano. Per questi ultimi, l’analisi si concentra sui potenziali errori operativi in fase manutentiva. Per questo motivo non vengono analizzate possibili interazioni per esempio, con le sostanze trasportate dal treno.
L’analisi di sicurezza viene solitamente svolta come valutazione del rischio. in questo studio RAMS la probabilità che si verifichi un tale evento viene quantificato in base a due fattori: la probabilità che di accadimento e l’entità delle conseguenze. A tale proposito, la normativa EN50126 propone una matrice di rischio apposita.
Unisciti agli esperti
Oppure scopri il CMMS mainsim in meno di 3 minuti con questo video.
Ricevi i migliori consigli di manutenzione una volta al mese.
Unisciti agli esperti di manutenzione. Ricevi nuove risorse una volta al mese direttamente nella tua casella e-mail. E puoi annullare l’iscrizione quando vuoi.