Che cos’è la manutenibilità?
Quando ricerchiamo su Google il significato della parola “manutenibilità” vengono proposti principalmente articoli accademici ingegneristici rivolti agli addetti ai lavori e non di facile comprensione. Ma tra dati, numeri e formule può sfuggire il significato di questo termine, che sembra quasi portare avanti una vera e propria missione.
Il concetto di manutenibilità si applica a partire dalle primissime fasi della progettazione, durante le quali si inizia già a tenere conto di come un domani sarà possibile manutenere l’asset o l’impianto e alla facilità con cui le attività di manutenzione possano essere eseguite.
Lo scopo della manutenibilità è quello di misurare la probabilità che un asset in uno stato di guasto possa essere ripristinato alle normali condizioni operative dopo aver subito la manutenzione.
In poche parole, il concetto di manutenibilità abbraccia tutto il ciclo di vita di un determinato asset più o meno complesso, tenendo conto che inesorabilmente prima o poi necessiterà di interventi di manutenzione. Per questo motivo, ad esempio, le parti principali non dovranno essere irraggiungibili dagli operatori o non ci dovranno essere troppi componenti critici complessi che possano rendere difficoltoso e più lungo l’intervento.
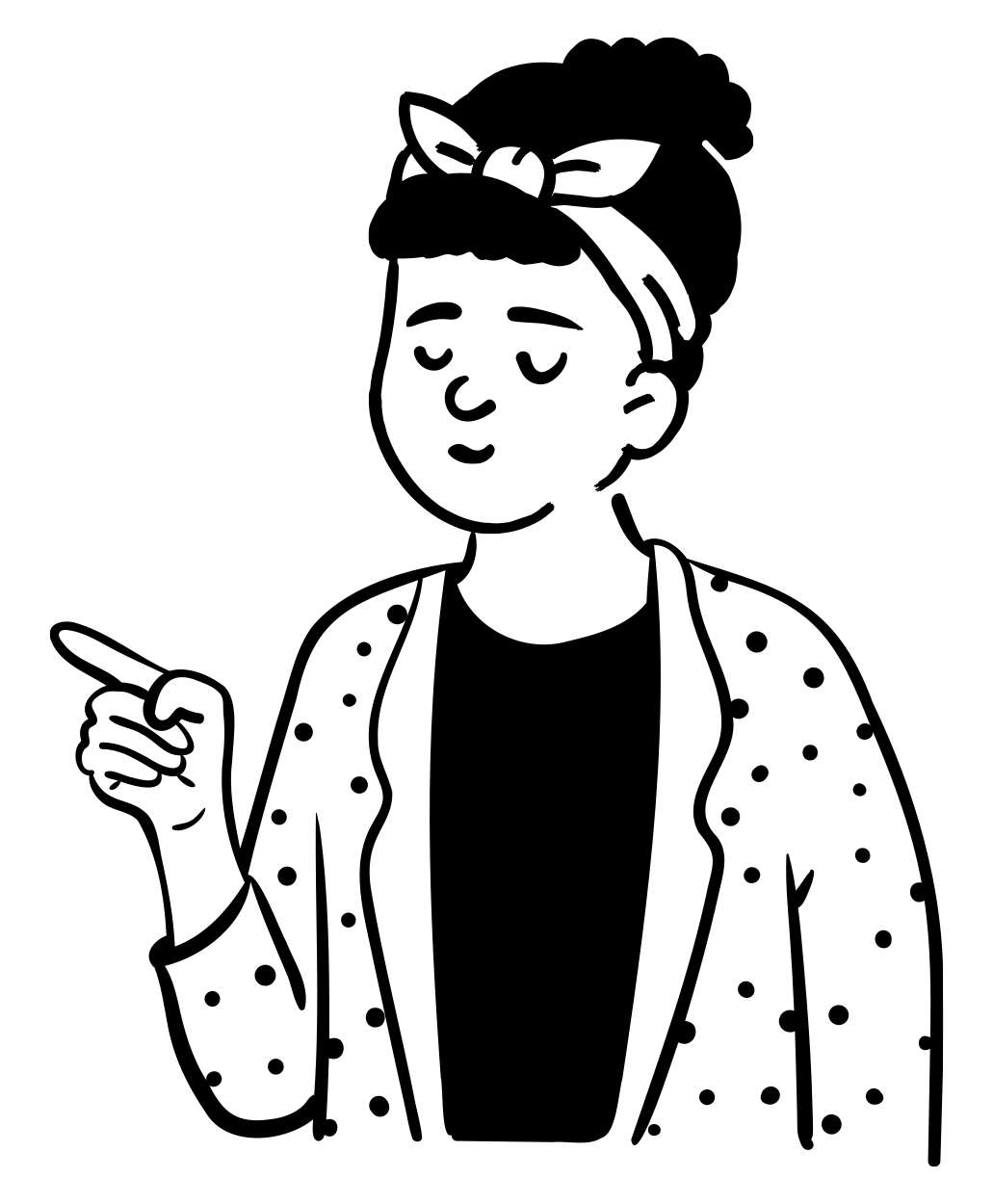
Condividi l’articolo
Indice dei contenuti
Come si misura la manutenibilità?
Per misurare la manutenibilità di un asset, un impianto o un macchinario è necessario essere in grado di quantificare la quantità di impegno dedicato all’esecuzione della sua manutenzione.
Se ti sembra familiare è perché il metodo più comune e semplice per questa analisi è quello di misurare il tempo medio di riparazione, ossia l’MRT.
Per calcolarlo dobbiamo semplicemente prendere il tempo effettivo di riparazione dell’asset e dividerlo per il numero di guasti che ha riportato quell’asset.
Altra metrica importante da considerare quando si parla di manutenibilità di un impianto è quella relativa il tempo medio tra due interventi di manutenzione (preventiva o a guasto), ossia il MTBM.
Questa metrica non tiene in considerazione il tempo di fermo macchina o dell’impianto comprensivo del guasto, ma è una media statistica dei tempi di disponibilità tra un intervento di manutenzione e l’altro, ossia l’improduttività a causa del guasto ma anche quella indotta dalla manutenzione programmata.
Il calcolo del MTBM fa si che l’Ingegneria di Manutenzione esegua un’analisi riguardo la progettazione del macchinario considerando appunto i periodi di fermo programmati e quindi la possibilità di riduzione degli stessi.
In poche parole, lo studio della costruzione di un macchinario o di un impianto deve avere come principio cardine quello di realizzare un asset che potenzialmente possa non necessitare di interventi di manutenzione a causa di guasti, e che la manutenzione programmata diventi sempre meno necessaria.
La manutenibilità degli impianti
Definizione di manutenibilità
Il termine manutenibilità in ambito industriale può voler significare da un lato la facilità con la quale è possibile intervenire su un asset, e dall’altro la probabilità che un’azione correttiva si renda necessaria in un determinato lasso di tempo.
Progettazione e manutenzione
Durante la fase di progettazione, il progettista attraverso la definizione delle caratteristiche costruttive e funzionali di un asset – come l’accessibilità, la sicurezza e l’ergonomicità – verifica l’attitudine di un impianto ad essere manutenuto, rendendo così la manutenibilità una caratteristica intrinseca del progetto.
Per assicurare la corretta gestione della manutenzione è necessario procedere inoltre ad una verifica della manutenibilità ogni volta che si applica un cambiamento alla risorsa, ossia occorre verificare se i tempi standard di intervento previsti siano effettivamente rispettabili.
I parametri di manutenibilità per gli impianti
Un impianto o un asset in fase di progettazione per essere definito manutenibile dovrà rispettare le specifiche di 7 parametri:
- dovrà essere accessibile, ossia essere progettato in modo che ogni sua parte permetta ispezioni e riparazioni in modo agevole. Le verifiche di queste caratteristiche possono essere effettuate tramite sistema BIM.
- si dovrà poter sconnettere ed asportare ogni componente o comunque quelli più importanti, senza che vi sia necessità di rimuoverne altri;
- i componenti soggetti a smontaggio per operazioni di manutenzione dovranno essere progettati in modo da essere facilmente trasportabili;
- le parti dell’asset devono poter essere progettate per facilitare al massimo le attività di pulizia;
- è buona norma tendere a standardizzare la tipologia di componenti e diversificare il meno possibile le apparecchiature in modo da avere un livello più alto di intercambiabilità;
- ogni componente deve poter essere sostituito da uno equivalente, senza effettuare modifiche tecniche di installazione.
- test e letture di dati devono poter essere fatti con semplicità.
Manutenibilità nella progettazione
Oltre a questi parametri che sono da considerare basilari per la progettazione degli asset principali, occorre anche considerare le caratteristiche relative l’operabilità, l’affidabilità, la disponibilità e la sicurezza, presenti nell’analisi RAMS.
Manutenibilità nella fase di avviamento
Lo scopo in questa fase è quello di verificare quanto la progettazione abbia tenuto conto delle esigenze della manutenzione.
La maggiore durata degli interventi si riflette sul piano di manutenzione comportando un aumento e allungamento del carico di lavoro.
L’analisi ha come requisiti di valutazione i parametri di accessibilità, estraibilità, manipolabilità, pulibilità e testabilità visti precedentemente e come specifiche le metriche di calcolo e i livelli di valutazione predefiniti.
Metodo FMA
Il concetto di manutenibilità è entrato a far parte dei criteri di progettazione nel momento in cui si è reso necessario considerare l’intero ciclo di vita dei costi di un asset (il Life Cycle Costing). Per fare questo, oltre al Capital Expenditure (CAPEX, ossia gli investimenti iniziali), è stato necessario tenere in considerazione anche la parte più sostanziale dei costi, ossia quella relativa i costi operativi, di manutenzione e dismissione (OPEX, Operating Expenditure).
Questi studi però anche se portati avanti fin dalle prime fasi progettuali, portavano a risultati ben lontani dagli scopi specifici della manutenzione, fornendo solo indicazioni qualitative.
Per questo motivo il Metodo FMA (Field Maintainability Analysis) ha come scopo quello di valutare l’impatto negativo della progettazione sulla manutenzione e di individuare le apparecchiature che necessitano di interventi migliorativi per aumentare il tasso di manutenibilità con i relativi costi.
Per realizzare l’analisi FMA è utile definire un piano di manutenzione preventiva nel quale vengano definite le seguenti attività:
- configurazione dell’impianto
- realizzazione delle istruzioni di lavoro per le attività di manutenzione
- definizione del piano di manutenzione preventiva (ossia associare ad ogni asset oggetto di manutenzione, le relative istruzioni e MTTR)
Successivamente, per sviluppare il metodo FMA sarà necessario attuare le seguenti fasi:
- PDefinire i parametri caratteristici di manutenibilità (PCM)
- PIdentificare le tipologie di apparecchiature più significativi (TAS)
- PAssociare ad ogni apparecchiatura chiave (TAS) i propri parametri (PCM)
- PEffettuare una valutazione sul campo dei tempi di intervento sulle TAS
- PConfrontare i risultati dei tempi testati con quanto descritto nelle istruzioni standard
- PCalcolare gli eventuali tempi da correggere
- PIndividuare le apparecchiature difficili da manutenere e valutarne i costi rispetto a quelli standard
- PDeterminare le migliorie da apportare
- PValutare la fattibilità di queste migliorie
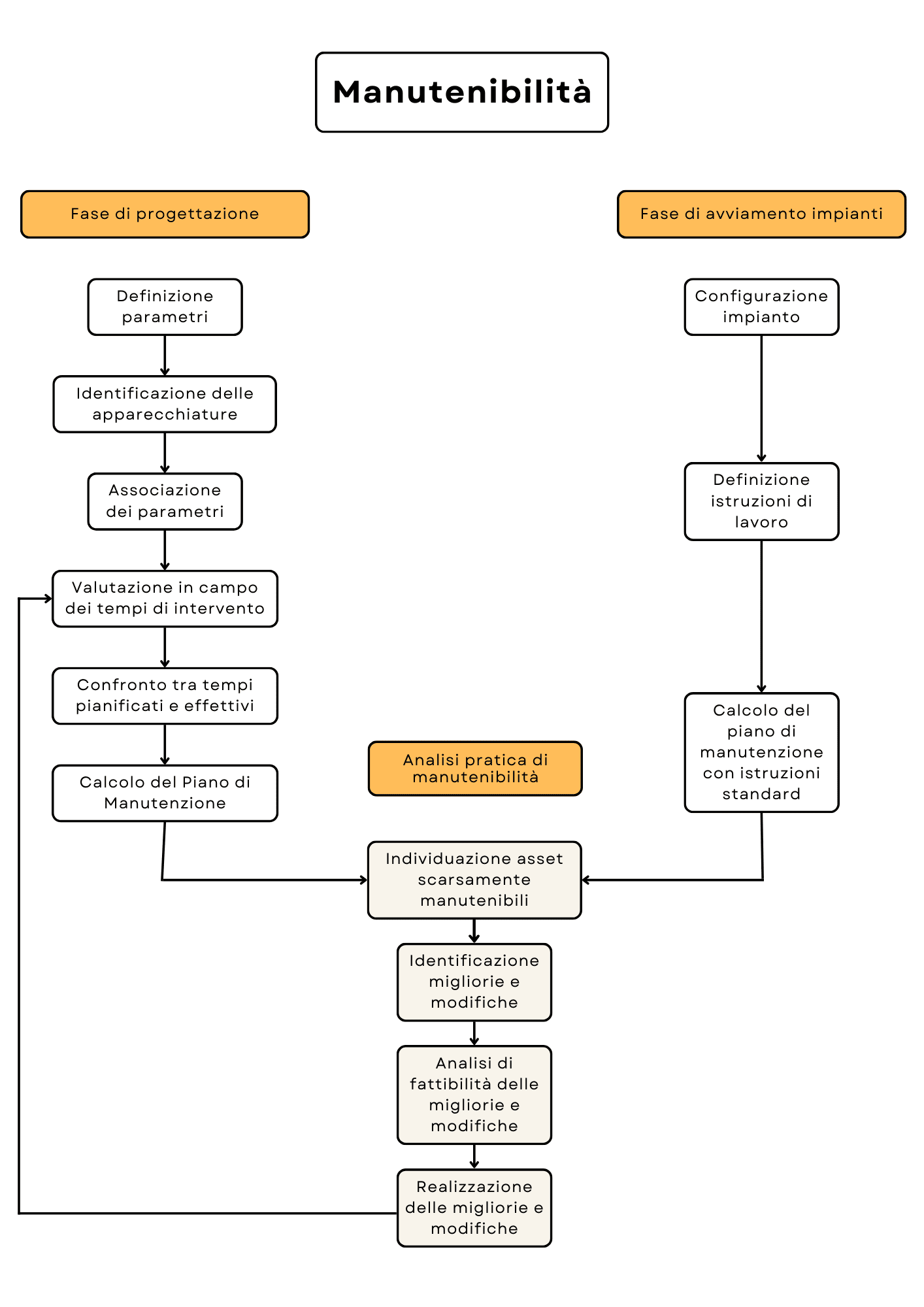
Su quali asset utilizzare il calcolo FMA
Come detto, il metodo di calcolo FMA è da ritenersi indicato per quegli asset che risultano fondamentali all’interno degli impianti produttivi.
Dovranno essere quindi quelle apparecchiature che ritroviamo più diffuse all’interno dell’impianto, che abbiano tempi di manutenzione preventiva significativi e che necessitino di interventi frequenti durante l’anno.
La scelta di queste peculiarità per l’attuazione del calcolo FMA è necessaria per far si che il carico di lavoro annuale sia consistente rispetto all’impegno economico che potrebbe derivare da eventuali attività di manutenzione extra.
Analisi dei risultati
L’impatto della manutenibilità riveste dunque un ruolo rilevante sulla manutenzione in termini di ore necessarie all’esecuzione dove la valutazione è da affidare alle tempistiche standard della manutenzione preventiva.
L’obiettivo del calcolo della manutenibilità in definitiva è dare una visione chiara e concreta delle ore di lavoro extra necessarie per manutenere gli asset a causa di una scarsa ingegnerizzazione in ottica manutentiva.
A tali costi però, bisogna anche aggiungere quelli dovuti alle ore dedicate alle verifiche e alle azioni correttive, oltre che a quelli incontrati per l’utilizzo di mezzi e attrezzature.
L’applicazione di questo metodo è particolarmente significativa se effettuata prima dell’avviamento di un grande impianto. Una maggiore precisione nella definizione del piano di manutenzione comporta infatti una migliore stima del budget di manutenzione che è lo strumento fondamentale per le scelte tecnico-gestionali di manutenzione. Il metodo FMA può anche costituire la base di partenza per definire i termini economici di confronto per gli eventuali costi dei lavori di migliorie e modifiche di impianto che si intendano realizzare. In tal caso l’applicazione del metodo rappresenta un investimento che produce benefici immediati. Il metodo FMA, infine, può essere utilizzato per definire le specifiche tecniche di manutenibilità delle varie tipologie di apparecchiature che l’ingegneria, in fase di progettazione degli impianti, deve rispettare al fine di tener in debita considerazione le esigenze della manutenzione e di minimizzare i costi di esercizio e manutenzione.
L’applicazione del metodo rappresenta un investimento i cui benefici sono differiti ma estesi lungo tutto l’arco temporale del ciclo di vita dell’impianto.
In che modo il CMMS può aiutare a migliorare la manutenibilità
Come abbiamo visto, lo studio della manutenibilità di un impianto o di un macchinario riguarda molti aspetti dell’Ingegneria di Manutenzione e della manutenzione stessa.
Per poter raccogliere e analizzare i dati e monitorare le metriche di manutenzione è necessario quindi dotarsi di uno strumento che sia in grado di restituire delle analisi attendibili e agevolare il lavoro dei manutentori.
Un Computerized Maintenance Management System (CMMS) è lo strumento in grado di aiutare a monitorare e tenere traccia delle metriche viste fin ora.
L’acquisizione in tempo reale dei dati relativi a tutto quello che accade a macchinari e impianti come il tracciamento delle ore di lavoro, il numero di interventi manutentivi, il tempo medio di risoluzione tra i guasti (MTTR), il tempo medio tra due guasti (MTBF) o le ore destinate a manutenzione programmata o preventiva, rendono il software CMMS lo strumento chiave per consentire di prendere decisioni data-driven, contribuendo alla riduzione dei tempi di intervento, fermo macchina e conseguente riduzione dei costi sostenuti dall’azienda.
Unisciti agli esperti
Oppure scopri il CMMS mainsim in meno di 3 minuti con questo video.